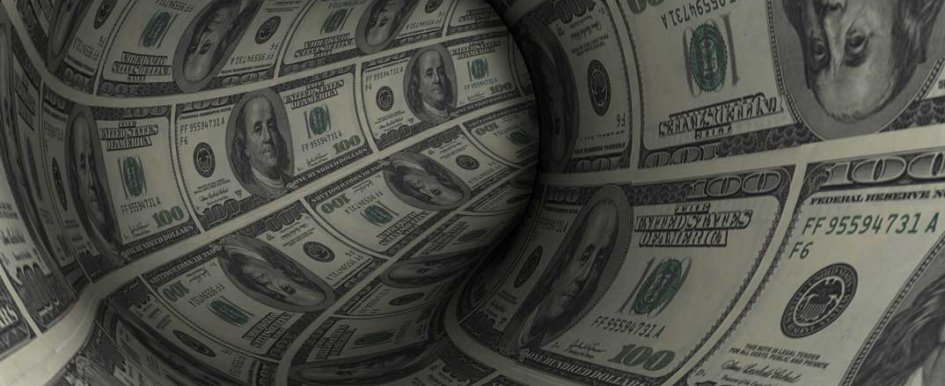
For nearly every heavy construction company, the unpredictability of maintenance costs is not unlike falling down the rabbit hole in Lewis Carroll’s famous story, Alice in Wonderland. Of course, this hole has serious ramifications that negatively impact the present and future bottom line. More companies are finding innovative ways to crawl out of that reactionary maintenance hole by developing and implementing comprehensive maintenance programs that suit their daily jobsite operations.
Some of the best of these programs are based on the predictability and comprehensive approach of total process reliability (TPR). This maintenance approach brings holistic structure and predictability that can deliver major improvements and changes to companies that implement it correctly.
One company that has already found success with TPR is Baker Rock Resources, an Oregon-based aggregate and paving materials supplier. The company is in its third full year of implementation of a TPR program, and has seen major changes and cost savings.
The company has gone from a 50-percent emergency breakdown rate to a rate of just over 1 percent in 2016. How they found success is a study in commitment and business cultural change that can be easily replicated by others.
The Challenge
Founded in 1956, the family-owned company and its more than 100 employees supply aggregate and paving materials to Northwest Oregon via divisions in Beaverton, Dayton and Molalla. Through ongoing relationships with major and minor road and construction projects throughout the state, Baker Rock’s main Beaverton quarry spans 250 acres and processes an average of 1.5 million tons of aggregate per year.
Like most major heavy construction companies in the United States, Baker Rock’s inefficient maintenance processes were suppressing true gains in maximized uptime, productivity and future growth.
According to Baker Rock Equipment Division’s Director Brian Young, the story is common across the construction industry where companies think operations are fine, yet they are falling down the rabbit hole of reactive maintenance. “Like many companies, we were constantly chasing problems and money with a tremendous amount of emergency repairs and downtime,” said Young.
Heavy equipment operators often see vendor labor as being highly trained with the latest tools, techniques and practices, but prohibitively expensive. This leads many companies to having an in-house labor force that suffers from an unconscious lack of efficiency. The reality is that it doesn’t have to be that way.
Discovering the Solution
The first step for Baker Rock was realizing that there is a problem to remedy it, which was an understanding that came from the top. For Baker Rock CEO Todd Baker, that realization came from a specific incident at their maintenance facility in 2011. After a piece of angle iron that had been left near the maintenance shop for some time punctured a company truck tire as it was exiting, Baker had reached his limit with inefficiency and reactive maintenance.
Baker remembered a presentation given by Preston Ingalls, of TBR Strategies, 8 years before and put thought into action. TBR Strategies, a Raleigh, North Carolina, maintenance and reliability consulting firm had a successful track record implementing total process reliability (TPR). “I had been intrigued by TPR, but at the time, I didn’t feel that we were in the right place as a company to take it on, but the incident irritated me so much that I knew it was time for a change,” said Baker.
As an outgrowth of principles devised by Japanese Engineer Seiichi Nakajima called total productive maintenance (TPM), TPR is about increasing equipment reliability, decreasing downtime and creating a unified asset management process by engaging the entire organization. For the three basic principles of TPR, see the box on page 61.
Forming A Maintenance Program or Process
The Baker Rock team began a process of overhauling existing processes, such as oil analysis, preventive maintenance (PM) procedures and service policies to bring them in line with new technology standards. This happened in conjunction with new process implementation for operator care, process guide development, inventory control, auditing, FMEA, root cause analysis and key performance indicators (KPIs).
The company established a training schedule and invested in tooling, computer diagnostics equipment, compression adaptors and hydraulic test kits.
“Among the processes brought to us by TBR was 5S, which set a visual and physical standard for shop cleanliness and organization,” said Young. 5S focuses on organization and orderliness of the workplace.
“[TPR] is a very holistic approach that starts at the leadership level and continues through to the newest employee,” said Young. “Consequently, it took the leadership and commitment from Baker Rock President Todd Baker to initiate and invest in it, as well as to have the patience to see it through to fruition.”
Baker, for his part, explained his ongoing role. “TPR is an [integral] part of what we do now, but that took constant reinforcement in the first couple of years, but in the ensuing 3 years, it’s become foundational to the business,” said Baker.
Old school technician productivity structures equated wrench turning alone with productivity, but the shift to training and education to learn new techniques to be functional teams would ultimately be more fruitful and efficient on the back side.
Changing the Culture
Both Baker and Young were quick to point out how a maintenance program based on TPR is a cultural change for the business, where the plan, goals, roles, expectations and feedback are built into the business. The company initiated a check sheet as part of the process to ensure follow-through. “You need leaders and managers willing to coach and mentor, because process and procedure change requires that type of accountability; without it, you are going to have a slow change process,” said Young.
To foster that cultural change, Baker personally attended 5S and CLAIR events. This type of attendance by leadership includes the executive staff, which rotates through bimonthly program meetings. “Rather than talk a lot, I mostly observe, and, at the end, I try to reinforce our commitment and how big a part they are playing in the TPR program,” said Baker.
Finding Program Results
While costs were higher for the initial PM cycles of the equipment, within 6 months, the machines with the highest PM cycles were showing financial gains in terms of lower maintenance costs and emergency repairs. This continued to improve throughout the first year and thereafter. “By our third year with the program in full swing, repair costs were really dropping and the emergency rate continues to drop to the current 1 percent,” said Young.
One of the key benefits was a major reduction in standby equipment. For example, the company had purged boneyard equipment at the start of the process and scraped six small rollers that averaged no more than 200 hours per year.
These were replaced with two new, small rollers that would immediately be part of the new maintenance program. A turn schedule was implemented that would introduce additional new rollers, which will continue to save on parts and maintenance costs, as well as downtime due to the maintenance program. As the maintenance program took hold and breakdowns disappeared, other benefits became apparent, such as comments from the community, customers and government agencies regarding the near pristine look and operational efficiency of the equipment and facilities. This would bring tangible results in terms of being far more competitive in the marketplace.
While the benefits of TPR and a successfully implemented maintenance program is huge in terms of cost and time savings as well as overall company efficiency, it is a major undertaking.
Baker made it clear that this commitment starts with company leadership, but must have full buy-in from the staff.
“The owner, as well as the executive team, must be committed to process implementation and be ready to figure out how to maneuver through the inevitable bumps in the road,” said Baker. “Ultimately, the key is having good employees, as nothing gets done without their buy-in and cooperation. We make TPR part of everyone’s job, so when employees are scheduled for training, managers are responsible for scheduling a way to fill that time in the field and ensure that the employee goes to training.”
Creating a Future Maintenance Wonderland
Currently, the company is optimistic about the future results for their emerging training program in cooperation with local colleges and vendors to deliver factory and systems theory training to employees.
While the future is bright for Baker Rock, getting to a true maintenance wonderland takes hard work, open communication, commitment to change and, most of all, clear planning and direction.
On Young’s office wall is a quote that he references throughout his day from Carroll’s Alice in Wonderland, “If you don’t know where you are going, any road will take you there.”
“If you don’t believe in the vision that you have created, and you don’t communicate that with your team and your organization, you are never going to get there. In the ongoing journey, it is vitally important to measure everything, work on continuous improvement, never rest and never settle, because there is always a way to improve what you are [currently] doing.”
3 Principles of Total Process Reliability (TPR)
- Detection—Use preventive & predictive technology to inspect, detect & correct small defects before they become costly.
- Restoration—Restore equipment to optimal conditions as it is needed.
- Prevention—Prevent small defects from becoming major problems by correcting them before they become costly repairs.