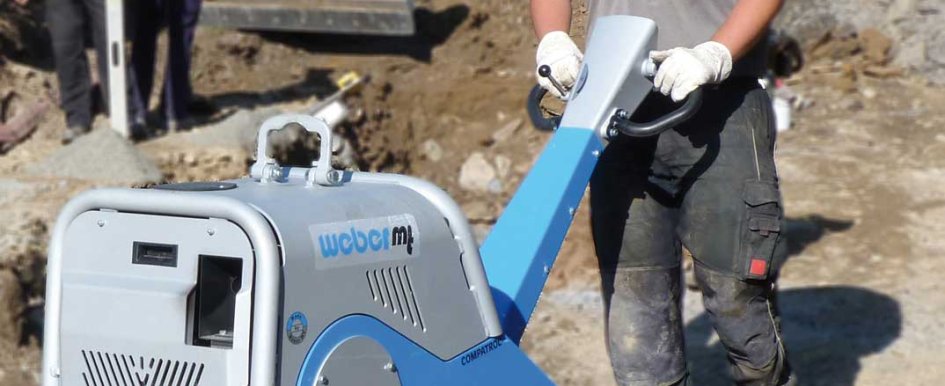
Compaction equipment is not always the most favorite equipment on the jobsite, but it should be. Soil compaction is a critical component in construction. Compaction reduces the voids in the soil material to create a solid foundation for the project, and it ensures the durability and stability of the structures being supported. Proper compaction means increased load-bearing capacity, higher density of the soil, reduced water permeability and elimination of frost damage. Often, the structural failure of projects and the damage caused by foundation settlement is due to improper soil compaction. Therefore, buying or renting the right compaction machine is paramount to the success of the job. Use the following questions to determine which investment will earn you the highest potential ROI.
1. Which machine is best for which soil type?
The two main soil types to consider when buying a compactor are granular and cohesive. Forward plate compactors, reversible plate compactors and vibratory rollers are best used for granular soils, since they operate by vibrating or shaking the particles into place. The size of the machine depends on the size of the particles. Smaller particles require higher frequencies and may have lower compaction forces, while larger particles require lower frequencies, but have higher compaction forces.
2. How can I save on labor?
Becuase labor makes up the largest portion of the variable cost for most jobs, it is wise to look at the details of the equipment to make sure operators are utilizing their time efficiently. Many contractors end up saving on the initial cost of equipment, but paying 10-fold in labor costs due to inefficiencies of product choice. The biggest advantage of using a reversible plate over a forward plate is time. Reversible plates are easier to maneuver, especially in tight corners. Also, larger machines have bigger engines and offer more compaction force and larger surface area of the base plate, making them faster than forward plate compactors. Find out if the machine comes with extension plates or if they are available at an additional cost. Plate extensions increase speed and productivity, but removing them can be important when working in tight spaces.
While a larger surface area is important when deciding between a reversible plate and a forward plate, beware of reversible plates with large, flat surface areas. The large, flat surface acts as a suction cup, preventing proper speed and grade. Some manufacturers have found that, on some models, reducing the surface area increases the speed. Just because the plate is larger does not always mean it is faster.
Another important factor regarding cost/productivity efficiency for a reversible plate would be a service indicator, which lets you know when there is an issue with the machine. Some larger reversible compactors offer built-in systems, which inform users of important service-related issues. While frequent servicing of minor issues may be time consuming and hold up a job for a few minutes, it is nothing compared to the time that is needed should a more significant issue occur to the engine. Keeping that in mind, it is important to make sure that all maintenance points, as well as regular usage points, are easily accessible and can be repaired with ease, right on the jobsite. Another time-saver would be a compaction control meter, which can be found on some large reversible plates and helps the operator know when optimum compaction has been reached. However, make sure the meter is proven to create accurate measurements.
3. How can safety concerns impact my decision?
No matter what compactor you are considering buying, make sure the machine and operator will be well protected. These machines get beat up, perhaps more than any other piece of equipment. Checking to make sure there is a rugged protection frame surrounding the engine, as well as shock mounts throughout the machine, is paramount. Unfortunately, perception is sometimes reality, and operators assume the more they can feel the impact of the machine, the harder it is hitting. A good compactor ensures that the impact is going where it should go: into the ground and not into the operator. Ergonomics should be a priority with any piece of equipment. For compactors, this means that the guide bar should be lockable and adjustable to the operator’s height.
Anti-vibration handles are available on some models, which also alleviate the stress on the operator. Power to weight ratio is an important factor when thinking of operator safety. Many people look for a compactor according to its weight, but what they should really look for is how much compaction force the machine gives out. It is best to find a compactor that weighs less, but has more power.
4. What should I know about machine exhaust?
The exhaust should be located away from the operator, in the front of the machine and not on the sides, to avoid soot getting on walls during operation. To ensure better control and performance, make sure that with forward plates or reversible plates, the eccentric is built into the base plate. You will not have to worry about replacing bolts.
5. What technical aspects should I consider?
The following points are other critical considerations when you are looking to purchase your next plate compactor.
A. Forward plates
- The size of the water tank saves you time in the end. Make sure you inquire about how much water the tank can hold and how it is mounted. Test whether or not the water really does end up on the asphalt and not on top of the plate. The closer the hose or sprinkler is to the base plate, the higher the chances the spray function will work. If you want to find out, hang the machine and turn it on. The vibration of the machine will show you how the water will flow.
- Wheel kits are a must, but if they are too thin and made of a low-grade plastic, they could end up being more of a hassle. Make sure the wheels are inflatable and wide enough to maneuver through rough terrain.
- Anti-vibration handle bars increase productivity and protect the operator.
B. Reversible Plates
Look for a compactor with hydraulic shift with infinitely variable speed—you only have to move the handle back and forth, making it safer and easier for the operator.
- Is the clutch self-adjusting?
- The throttle cable should be protected within the guide bar to avoid damage.
- Choose a compactor with a foldable lifting eye, so it is not in the operator’s view and makes transport easier. Also look at the construction of the lifting eye to make sure it is sturdy.
- Does the base plate have flat edges so that dirt is able to vibrate off and not get stuck on the machine?
C. Rammers
- How many speeds on the throttle? Look for a machine with three speeds.
- Is there a strong steel protection over the engine? How is the visibility? The steel cover should be a separate component so the frame does not hit the engine when vibrating.
- What is the filtration system like? Can you check and change filters easily?
- Narrow bellows allow for longevity in narrow trenches.
- The base plate should be protected to avoid wear.
The most important thing is to do your homework. When seeking your next plate compactor, be sure to ask the questions listed above in order to be on a solidly compacted road to success.