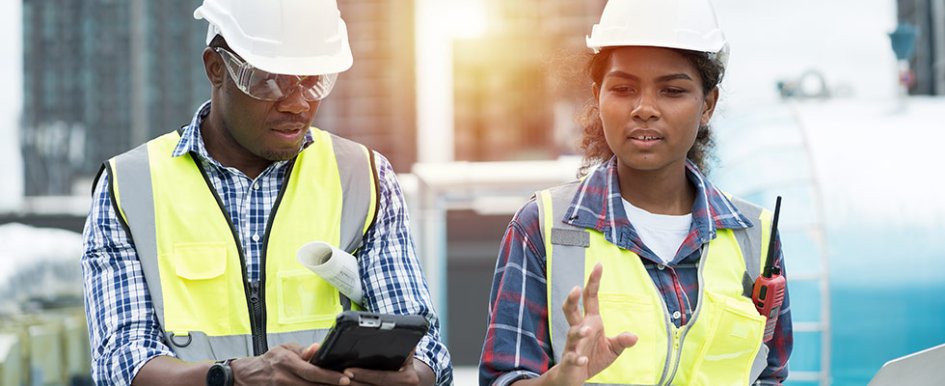
When it comes to green building, many people think about incorporating energy-efficient features such as effective insulation and glazing, adding eco-friendly lighting or using recycled or repurposed materials. All of those are important, but it’s also important to step back and think about the construction process itself. Above all, it’s vital to find new ways to leverage digitization and new technologies to make our work more sustainable across the entire building life cycle.
Since 2005, America’s stock of Leadership in Energy and Environmental Design (LEED) certified buildings has grown twentyfold, and with energy prices soaring and corporations, policymakers and consumers all pushing for a greener built environment, the trend shows no sign of slowing. But we still have a huge hill to climb. Buildings are responsible for almost two-fifths of all global greenhouse gas emissions and nearly one-third of total global energy consumption, so ushering in a new era of sustainable construction will take a new, whole-life-cycle approach to designing, constructing and operating buildings of all kinds.
Digitization will have a key role to play in this process, from performing energy-usage calculations to enabling more informed choices around materials, waste, lighting, ventilation and more. The following are four key steps that we need to take to rise to the challenge.
1. Focus on Low-Impact Materials
Planning is key to any construction project, but with a sustainable build, careful forethought is vital. Long before the first foundation is laid, architects and site leaders should use digital tools to model and track the current and future impact of every decision they make — and that includes considering which materials align with the project’s sustainability goals, both in terms of immediate impact and longer-term factors such as energy efficiency.
Three commonly used building materials — concrete, steel and aluminum — account for a staggering 23% of global emissions. Fortunately, it’s possible to mitigate their impact. At the procurement stage, you can specify low-carbon concrete mixes or opt for so-called “green steel” — produced with renewable power and recycled feedstock — to reduce your project’s total footprint.
For some projects, of course, using alternative materials, from mud and straw to eco-friendly lumber, might be a better option. In other cases, digital technologies can be used to 3D-print parts and structures to order, reducing waste.
Of course, using innovative materials also means prioritizing communication such as messaging tools, app-based blueprints and task-management solutions to ensure that planners and construction teams understand the new processes and are able to run their projects in ways that deliver the desired results.
2. Clean Up the Construction Process
Because low-carbon construction often requires new materials and processes, it’s vital to ensure that all stakeholders in the construction process are sharing information and plans effectively. Mistakes or miscommunication that result in materials being discarded or structures being rebuilt can sharply increase the total environmental impact of a project, making it impossible to reach net-zero goals.
Of course, keeping sustainability goals front and center during a complex build can be tricky. Even at the best of times, building sites are frenetic places with a multitude of moving parts. From an environmental standpoint, this confusion can be problematic: Whether it’s the scope for locating heavy machinery in the wrong place or a misaligned section of insulation, there are plenty of ways for sustainable construction projects to go wrong.
On this front, digital construction platforms are also a huge asset, providing a common landscape in which designers, construction leaders and contractors can collaborate. Keeping things organized is essential in order to generate results, and proper documentation at every step of the process is vital as groups work toward LEED status or other environmental certification programs.
3. Prioritize Sustainable Operations
With more than two-thirds of a building’s lifetime environmental impact coming from the way it’s used, not the way it’s built, it’s important to think about your building’s lifetime environmental footprint. Rooftop reservoirs can harvest rainwater for use in cooling systems and bathrooms. Some properties use on-site solar panels, heat pumps and wind turbines to generate their own renewable power.
But you don’t have to make big upfront investments to make a difference. Simply swapping out incandescent bulbs for LED lighting can cut power usage by 75%, and properly maintaining and utilizing HVAC units based on real-time needs can also make a huge difference. Even something as simple as lowering blinds or keeping windows and doors closed can make a big difference to a building’s impact as well as its operating costs.
To manage a portfolio of energy-saving strategies, ranging from high-tech add-ons to low-tech maintenance and management workflows, it often helps to use digital tools to keep track of how everything is working. A low-carbon building is a finely tuned machine with many moving parts, and keeping everything running smoothly requires facility management platforms capable of monitoring and optimizing the performance of the system as a whole.
4. Don’t Forget About Decommissioning
Buildings don’t last forever, so it’s important to include end-of-life environmental impacts when you’re considering your project’s total carbon budget. Hopefully many projects will wind up getting repurposed rather than demolished: According to the American Institute of Architects (AIA), renovation projects can save up to 75% of embodied emissions — the total quantity of carbon dioxide produced during a structure’s creation — compared with constructing something new.
Sometimes, however, a building simply has to come down. That’s why the best green construction companies plan ahead and build in ways that make it easier to dismantle buildings and recycle materials. The more that can be salvaged from a project, the less its total environmental impact will be.
By using a digital solution to track every step of the design, construction and building management process, you can develop a single source of knowledge for all your building’s materials, structures and functional elements. When it’s finally time to decommission, that will make it far easier to reduce the whole-life-cycle impact of your property.
A Cradle-to-Grave Opportunity
Sustainable construction is booming — and that means businesses that act now and invest in the digital technologies and other innovative tools needed to realize net-zero and low-carbon principles across the entire building life cycle will be positioned to succeed.
To achieve meaningful results, win over eco-conscious consumers, and make sustainable building more effective and affordable, it’s vital to take a cradle-to-grave approach. Sustainability should be front-of-mind from the first time an architect fires up their design software, right through to the moment when a well-loved building is finally retired.
To make that happen, stakeholders at every stage of the construction and building management process must be willing to explore new ways of doing business, harnessing innovative techniques and technologies that heighten energy efficiency, reduce waste and facilitate the use of natural resources. Sustainable buildings have a bright future — it’s up to us to lean into digitization and find new ways to unlock their potential.