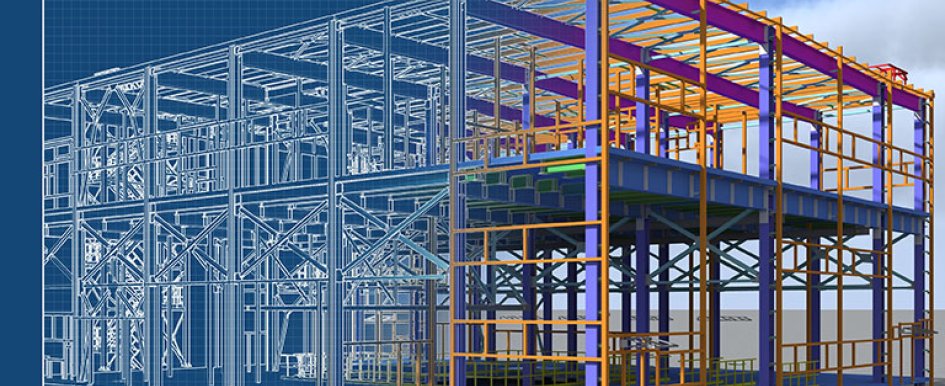
Most of us have probably heard the phrase “preconstruction is where you make your money” at some point in our career. An effective preconstruction process has typically been something of a secret weapon in the past – but as our industry begins to rapidly digitize, an increasing number of companies are more effectively connecting their preconstruction teams through technology. This connection allows for much stronger collaboration within organizations – speeding up delivery times and reducing errors that lead to costly rework – all before ground is even broken.
Bringing together the wide variety of stakeholders in the preconstruction process and catching errors early is crucial because making changes during construction is the fastest way to derail a project. In fact, the MacLeamy curve shows that the further along a construction project is, the more difficult and costly changes will become. In 2018 alone, rework on the jobsite cost the construction industry $31 billion.
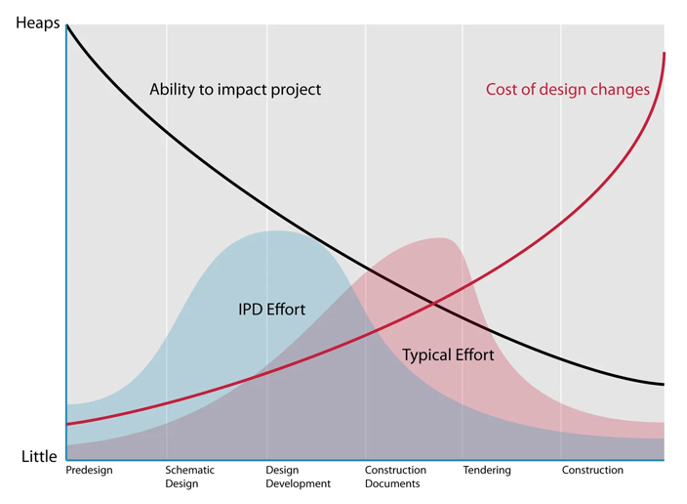
But lucky for the industry, Building Information Modeling (BIM) paired with the power of cloud technology can bolster preconstruction efforts and give connected teams the power to stay within budget and on time. To do so, general contractors and trades need efficient, accurate and collaborative tools.
From Design Intent to a Construction-Ready Model
While we often talk about BIM in the context of design, the value of BIM goes far beyond design and design intent. We’re seeing a growing number of teams utilizing BIM to connect design and construction teams through every phase of a construction project – which has proven to be particularly valuable during preconstruction. As companies become more nimble and begin adopting more advanced building techniques such as design-build project delivery (as opposed to a design-bid-build approach), using BIM to connect preconstruction workflows is helping unify multi-disciplinary teams to achieve continuous collaboration and solve constructability issues before they hit the field.
For instance, once a designer’s model is published in the common data environment and shared with the project team, the next step is for the BIM or VDC manager to coordinate with design leads and trade partners to identify and resolve constructability issues. From there, BIM data can be appended to the model. Then, detailed schedules are created, after which a quantity takeoff is performed to determine cost and quantity estimates. In this workflow, utilizing BIM models during preconstruction effectively gives teams a working model to iterate, track changes and ultimately improve on – all from one single location, in a format that the entire team can easily consume.
Bringing BIM Managers & Estimators under One Roof
In keeping with the adage of “preconstruction is where you make your money,” a big indicator of success during the preconstruction phase is the quality of collaboration between BIM managers and estimators – especially when you’re working with folks outside of your own company. Failure to collect and leverage data can lead to duplicated work, mistakes and wasted time – which has massive implications when these projects break ground. Case-in-point: research by Autodesk and FMI found that poor project data and miscommunication cause 52% of rework. Making BIM models available in a common data environment allows BIM managers and estimators to efficiently, transparently and collaboratively work together to get projects out the door faster with fewer errors.
There are also massive benefits in thinking bigger than just the project at hand – a common data environment will let you track historical data trends across all your projects. This empowers your decision-makers with insights to make the right decisions and help teams optimize for future projects.
Extending the Life of Your BIM Data in a Common Data Environment
When your entire construction process is organized through a common data environment in the cloud, it’s much easier to keep track of progress and critical information throughout the project’s lifecycle. Design iterations, RFIs, change orders, quantities, estimates and coordination issues are all recorded and referenceable anytime, anywhere, by everyone on the project team. Instead of juggling emails and spreadsheets, project teams can communicate directly through the CDE, creating a truly connected construction experience.
This also means that a detailed digital record of every component of a completed structure — including information on the process that structure underwent throughout construction — can be passed to the owner, increasing their understanding of the built asset they now own and empowering them to make better decisions.
BIM is the Connective Tissue of Preconstruction & Beyond
When you bring BIM into the preconstruction equation, what begins as a model to primarily express design intent becomes a construction-ready aggregated model that can bring clarity and value to the entire construction process. The same models that were quantified and coordinated during preconstruction can be continually referenced by the field team at the same time. In the same sense that the foundation of any building is what keeps it standing, using BIM during the preconstruction phase helps lay a solid foundation for projects and helps your entire team – regardless of the phase of the project – succeed.