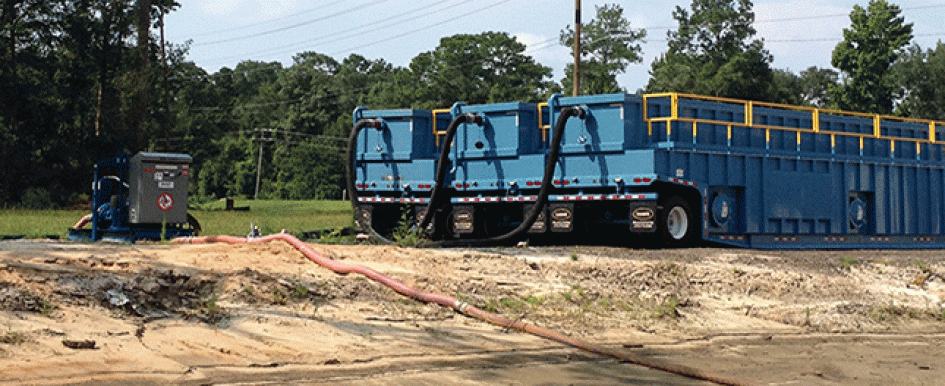
Dewatering plays a critical role in the success and safety of most jobsites and can pose a variety of challenges, which vary by jobsite. Some of these challenges include selecting the proper pump and accessories for the application, deciding where to discharge the water, managing jobsite water with limited space and doing so while abiding by relevant regulations such as those set by the Environmental Protection Agency (EPA).
Pump Application Checklist
The first step in developing a jobsite dewatering plan is to identify the required capacity, suction lift and discharge head at the site. The required capacity is the amount of fluid that needs to be moved and the rate at which it needs to be moved, measured in gallons per minute. Suction lift is the vertical distance of suction that the pump must overcome to bring the fluid into the pump. This distance is measured from the top of the pumping fluid to the height of the suction end of the pump. The discharge head is the vertical height of discharge hose or pipe. Once these factors have been calculated, you will be able to better determine the appropriate pump for the application.
Before selecting a pump for the job, evaluate the site conditions and answer the following questions:
- What does the pump need to accomplish?
- What type of liquid will be pumped?
- Will the liquid being pumped contain any solid matter?
- How far will the fluid need to be pumped?
- At what rate will the liquid need to be moved?
- Consider the jobsite environment—are there any special considerations, or will you need any auxiliary equipment?
- Will noise be an issue?
- Where on the jobsite will the pump be placed?
- Where will the liquid be discharged?
- Will the application require filtration?
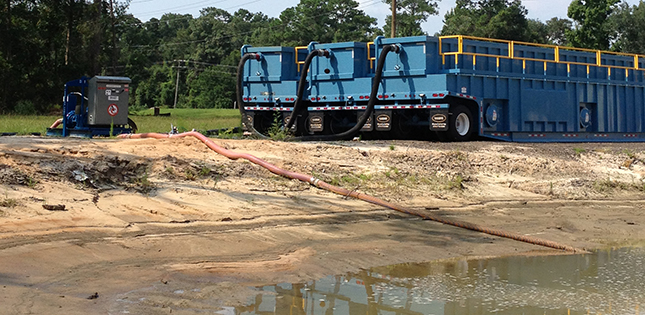
Types of Pumps
Pump capabilities vary from specialized to highly versatile and from low pressure to high pressure. Some are more capable of pumping fluid vertically than others, and, while some work well for moving water with debris, others will clog under those same conditions. A pump that is not designed to move solids may cost less, but it will likely clog and break if any type of debris is pumped through it. Choosing the correct pump for the application can help ensure a safe and successful job.
Portable trash pumps are most commonly used for jobsite dewatering, especially on jobsites that contain an open body of water that can be pumped via a pipe or hose. Trash pumps are available with a wet priming system, which requires the user to manually prime the pump by filling the casing with water, or a dry priming system that is equipped with a compressor or vacuum-assisted external priming system that primes automatically without adding water. These centrifugal pumps are ideal for transferring water containing solids and debris.
Diaphragm pumps operate by rubber diaphragms, which open and close inside the pump casing creating a vacuum to draw in water. Diaphragm pumps are ideal for muddy applications; however, they are not preferred for high-volume applications.
Wellpoint pumps are specifically designed and engineered for wellpoint and sock dewatering with high-air handling, large water volume and high-vacuum capability. Wellpoint dewatering is a simple method of temporarily lowering the groundwater table in a localized area to accomplish the construction of a foundation, pipeline or other structure. A wellpoint system consists of a series of shallow wells—called wellpoints—installed around the excavation and connected to a wellpoint pump by means of a set of header pipes with couplings and fittings.
Hydraulic submersible pumps consist of a hydraulic power unit, which drives the pump end that is submerged into the water. Hydraulic submersible pumps are ideal when a pump unit cannot be located next to the source.
Table 1 is a general pump selection table that identifies which type of pump is best suited for a specific application. You also should refer to the pump performance curve supplied by the pump manufacturer, which will show the capabilities of the pump at different volumes and will match the correct size pump to meet your flow requirements.
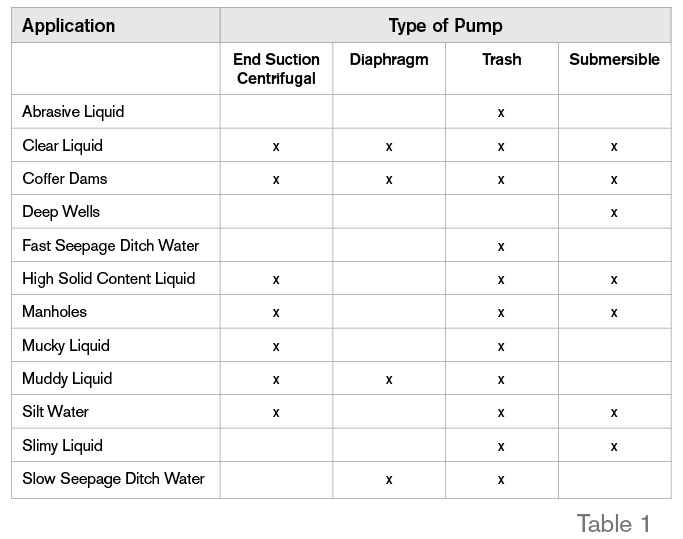
In most cases, a pumping system is not complete without the required accessories. Generally, suction and discharge hoses or pipes are required in various lengths specific to the application. These hoses and pipes will also require fittings to connect to the pump and may require additional fixtures such as valves, reducers, manifolds and couplings. Other pump accessories include sound-reducing canopies to decrease the noise level of the operating pump; driveway crossings to allow traffic to pass over discharge hose without harming the pump operation; auxiliary fuel tanks for pumps powered by natural gas or liquefied petroleum gas; generators and variable frequency-drive panels for electrical driven pumps; and wellpointing accessories. Ask your preferred pump company if they provide these auxiliary items. Some pump companies will install the entire pump system for you.
Jobsite Challenges
Most pumps are trailer-mounted or skid-mounted. A trailer-mounted pump system is easily portable but may take up additional space on the jobsite. A jobsite lacking additional space would be better suited with a skid-mounted pump. Jobsites with limited space also present challenges such as finding a location to store or discharge fluids. Pay careful attention to where the fluid is being discharged. Under the Clean Air Act, the EPA requires filtration of fluids that are released into navigable waterways. Be sure to check for other local laws and regulations.
Groundwater containing solids or contaminants can also be filtered on-site using a sediment tank. A sediment tank is a portable container separated into compartments by weirs. Water is pumped into one end of the container, which is designed to allow the sediment-laden water to flow over and under a series of weirs, causing solids to fall to the bottom and resulting in clear water discharged from the opposite end. Portable sediment tanks are commonly used on jobsites that lack sufficient space and require water that is being removed from the jobsite to be free of sediment before being discharged into a stream or storm drainage system. Jobsites involving dewatering of groundwater that contains contaminants such as oil or gas may require further filtration through a stripping system. Additionally, active treatment systems can be used to regulate pH and reduce the turbidity of the water being removed from a jobsite to an acceptable level.
Space permitting, groundwater containing solids can be filtered on-site using a filter bag. Filter bags are made of durable geotextile fabric, which allows water to pass through while solids remain trapped inside the bag to prevent pollution at the discharge site. The filter bag is attached to the discharge hose of the pump, and groundwater is pumped into the filter bag, trapping solids in suspension and allowing the sediment-free water to gently discharge into a nearby stream or other body of water without polluting the waterway or causing erosion.
When immediate discharge of fluids being removed from a jobsite is not an option due to lack of a discharge location, fluids may be kept on-site in a tank that will later be hauled away to be filtered or discharged. Another on-site containment option includes storage of groundwater in a retention pond to be later infiltrated back into the soil, evaporated or used for dust control.