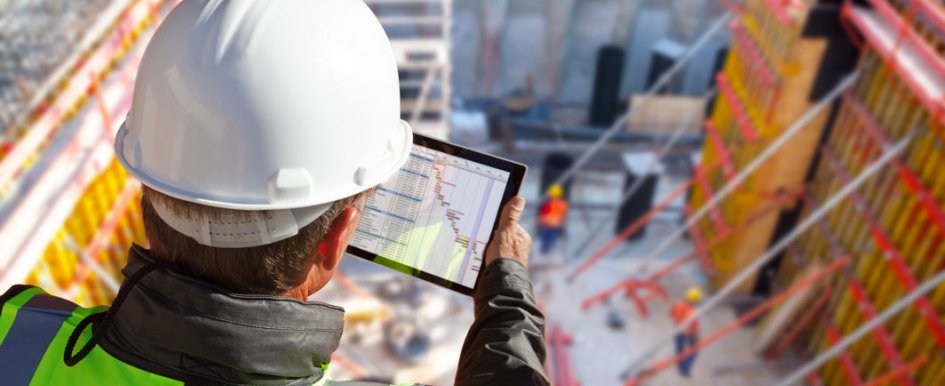
Today, contractors are faced with scheduling constraints from end users, a shortage of skilled workers, issues with jobsite workflow and organization, and low productivity. But could adding a dedicated materials planner alleviate these jobsite problems?
Materials management focuses on the optimization of construction site planning and organization and the movement of all tools and materials. As such, having someone committed to this role increases the value of a contractor and their profits.
1. Work Ahead of Schedule
Construction projects take a considerable amount of planning. One contractor’s poor planning can create a domino effect, impacting all trades on a project. Small initial delays can easily put the entire job behind schedule, costing money and creating frustration for contractors and the end user. Many construction projects use a pull-planning system to keep all contractors aligned, with the leaders of all trades present on regular project meetings used to appropriate, sequence and agree upon upcoming work tasks.
Material delivery has a substantial impact on a construction timeline as well. Time is wasted waiting to install equipment when vendors deliver a product later than scheduled. In pull-planning meetings, contractors work together to define the upcoming tasks for a time period, along with which materials will be needed. Issues with delivery schedules are identified and proactively addressed as a team so that work keeps moving forward.
The information from these meetings is disseminated by the trade superintendents to their planners, and tasks are broken down by person, per day, and are used to develop a 24-hour planner. As the name implies, 24-hour planners map out future tasks and the people responsible for those tasks over throughout the next day. These planners are used to:
- Communicate priorities set by the superintendent for their team without having to talk every person through their duties
- Provide materials planners with a guide for upcoming tasks so they can plan and organize the tools and materials needed and review inventory
- Provide a roadmap for the on-site logistics team, letting them know where work will take place so they can properly set up work areas and move materials to points of use
The 24-hour planner is a beneficial tool for keeping projects on schedule, especially for materials planners. Using the 24-hour planner, 1-week and 2-week planners, and a monthly schedule enables them to analyze short- and long-term inventory needs and work with vendors to schedule materials for delivery.
It is crucial that all parties, including general contractors, subcontractors, tradespeople, materials planners and all vendor suppliers, have effective communication to ensure the materials needed for each task are ordered and delivered on time.
2. Support Skilled Laborers
A skilled trade background and experience are not required for the materials planner position. Instead, they should understand the materials, how to order them and how to manage them when they arrive on-site.
Some companies may have similar positions referred to as “helpers.” However, many helpers are hired with the intent of moving into a trade apprenticeship. Consequently, these positions can have higher turnover rates.
A better option would be to hire someone with the intent of having them work in the materials management role and provide advancement opportunities for them, such as increasing responsibility on larger construction projects or having them train and manage more materials management professionals as the department grows.
3. Keep Sites Organized
Materials planners ensure the contractor has the right type and amount of materials in inventory, as well as the right tools for all upcoming tasks. They analyze project schedules and work directly with vendors and suppliers to audit the materials needed on-site and communicate when materials need to be delivered. They work with the on-site logistics team to move materials from a supplier delivery or a storage container to their point-of-use areas, often using just-in-time delivery (JIT) for skilled tradespeople to install the necessary materials.
Some companies work directly with their suppliers to assist with JIT delivery by implementing a vendor-managed inventory. Suppliers come in and audit the contractor’s available materials and the materials needed for upcoming tasks. Vendor-managed inventory helps suppliers increase productivity by allowing them to monitor the customer’s supply levels and plan production of the product accordingly.
Likewise, customers don’t have to worry about processing orders or running out of inventory because the supplier takes care of restocking materials. This strategy brings a team approach to the materials management and vendor/supplier relationship, which requires a high level of communication and trust.
JIT delivery also reduces the amount of materials on-site, either out in the open, exposed to the elements or in storage containers. Materials sitting on jobsites have a high potential for waste—the longer a product sits, the more likely the materials will be damaged or lost.
Sitting inventory also poses a safety risk, as the more a product must be handled or moved, the more potential it has to cause injury to a worker. Because materials planners work closely with vendors and on-site logistics to keep the flow of materials moving, they reduce excess material on construction sites.
4. Increase Productivity
One of the greatest aspects of having a materials planner is that skilled labor professionals on the jobsite can focus on the job they are being paid to do. And construction companies can measure the productivity of their employees by using time studies, tracking how much time is spent on primary tasks, secondary tasks and waste.
Primary tasks are the necessary, value-added work the customer pays for, such as laying concrete, installing electrical work and framing walls. Secondary tasks are defined as supporting work the customer is not paying for, such as moving materials to their point-of-use areas. Wasted time is time spent doing unnecessary, nonvalue-added tasks like waiting for material to be delivered, moving materials from one space to another without an intended purpose, and setting up or cleaning up a work area.
Time studies can show exactly how much a person is being paid for their time spent on nonproductive tasks and how much money is being wasted. One contractor focused its efforts on decreasing waste and secondary time, and its employees now spend about 65% of their time on primary tasks— far above the industry average of 42%.
Skilled trade professionals are generally paid at a higher level than helpers and materials planners; therefore, their time is more profitable for the contractor when it is being spent on primary tasks. Materials planners help decrease the amount of time skilled laborers waste and spend on secondary tasks, making the entire team more profitable.