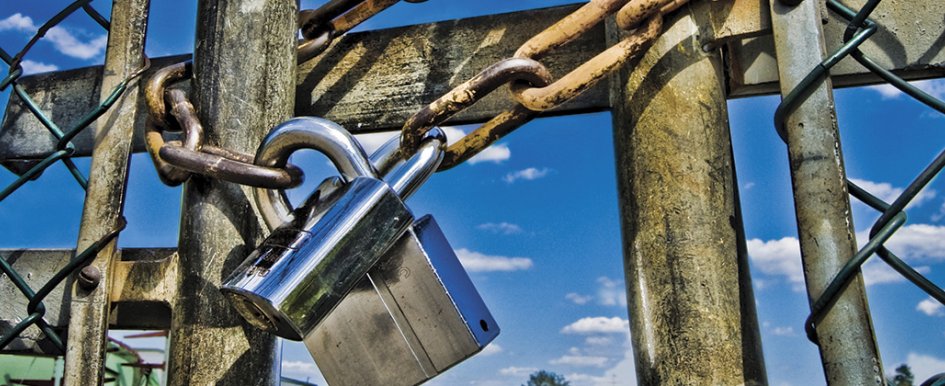
Backhoe and three trailers stolen overnight from construction site. Construction theft caught on tape, $30,000 in equipment missing. Job delayed due to major equipment theft. These are the headlines that appear in the media every day. However, because theft doesn't occur every day to every contractor or company, managers run the risk of thinking it "happens to other people" or "it isn't a risk in this state." Yet, construction managers must remain constantly vigilant, no matter their individual experiences, jobsite location or the perceived unlikelihood of thefts occurring.
According to the most recent report released by the National Insurance Crime Bureau (NICB) and the National Equipment Register (NER), a total of 11,625 heavy equipment thefts occurred in 2014, with just 2,633 of those machines recovered. The study estimates that the yearly cost of equipment theft is in the range of $400 million. That number does not even include major losses from business interruption. But construction business managers don't need to be a headline or lose valuable assets.
Theft is often preventable. Due to rapid technological advancements in telematics systems and tracking devices, it is now easier than ever to mitigate risk and keep equipment safe.
Information at Your Fingertips
In the past, the only way to assess a jobsite and discover missing inventory was for managers to physically walk through the site. This time-consuming process also lacks precision. On larger jobsites, less-utilized equipment could be missing for weeks before anyone noticed. Enter telematics. With a click of a button, contractors receive information about where all of their equipment is located, utilizing what was once a foreign concept, the Internet of Things (IoT), wherein objects have connectivity and can send and receive data. With telematics, construction business owners and managers are able to increase efficiencies over a broad operational range with immediate access to location data, without ever having to set foot on the jobsite. Because visits to the site are not always practical, telematics enables instant confirmation that all equipment is in the proper location.
Avoid Business Interruptions
Many crimes are reported after the fact, sometimes long after the perpetrators have had time to transport the stolen equipment across state lines. This is because theft is often not discovered until a certain piece of equipment is urgently needed by an employee or manager. Failing to complete a job on a timely basis due to theft can be killer to your bottom line. Avoiding possible job interruptions is a top priority for managers, and one of the most effective tools in telematics is an alarm module. In addition to location data, advanced telematics systems offer geofencing, unauthorized use/movement alerts and machine health notifications, all of which enable construction managers to set customized notifications.
Geofencing is used for equipment fleets when remote on a jobsite. If machines move out of that invisible boundary, regardless of the time of day or authorized employee presence at the jobsite, managers will receive a notification. This alert happens in real time, so managers are able to analyze the situation instantly and identify misuse by employees or a potential theft. This quick notification enables managers to alert the authorities within minutes, if needed, which makes equipment recovery considerably more likely. Alarm settings within the technology can also be utilized to assess employee mishandling or misuse, as managers will receive an alert if a machine is outside an approved area, moved a certain distance or running at an unscheduled time. It is also helpful as an inventory tool. Property can be managed and catalogued by the telematics system, simultaneously assessing that all equipment is exactly where it is supposed to be at any one time.
Making Informed Decisions
Telematics technology can act as a sort of business partner for contractors, providing the tools and insight needed to make major decisions that will support the company's success.
Telematics provides hard data, facts about multiple machines' locations throughout the day and reports on time spent idling the equipment. It is up to the business manager to make that data actionable, using his/her insight into the conditions on a job. For example, this technology could enable a contractor to see that three skid steer loaders are sitting unused and unattended during the hours of 2 to 4 p.m. each day in a certain locale near a major roadway. Knowing that loaders are one of the most commonly stolen pieces of heavy equipment, the savvy manager instantly sees the value in moving that equipment to a more secure location.
Telematics can often point out the weak spots in a theft protection plan or highlight a situation in which equipment could be better utilized. Managers are able to dive into the data provided by telematics and head off a loss before it occurs.
Ensuring Reduced Risk
While telematics is an essential tool in protecting assets, construction business owners and managers must also consider further steps to fully reduce risk. Criminals may be tech savvy and also know their way around a jobsite, so it is well worth adding additional theft-prevention technology. Installing unique trackers that go beyond simple GPS capabilities is a must-have, especially in high risk theft areas where thieves may store equipment underground for a period of time or in crates. It is also worth noting that the longer equipment is out of a business owner's hands, the larger the risk of damage.
Telematics, coupled with a tracking system, allows for faster recovery times, resulting in only minimal damage risk. While telematics is extremely useful in preventing theft before it occurs and aids in avoiding potential business interruptions, adding a second, reliable tracker ensures the company is doing all it can to prevent theft. With only 23 percent of stolen heavy equipment recovered in 2014, it is well worth going the extra mile.
It is easy to become overwhelmed when faced with the issue of risk management, especially when equipment managers are often in charge of large, complex jobsites and multiple machines. Using end-to-end technology solutions allows construction business managers to rest easy at night, knowing their jobsite won't be a headline in tomorrow's news.