Keeping projects and programs on schedule has always been a challenge for both owners and contractors. Delays are very costly and should be avoided if at all possible. Timely performance is commonly impacted by numerous factors, such as abnormal weather, funding, regulatory changes, public opposition, labor or material shortages, differing site conditions, and a myriad of other events that are outside the control of project participants. The following guidelines are recommended to meet these challenges and to keep projects on track.
Detailed Schedule Planning
Many projects fail to meet their goals because planning did not include establishing a realistic, achievable schedule.
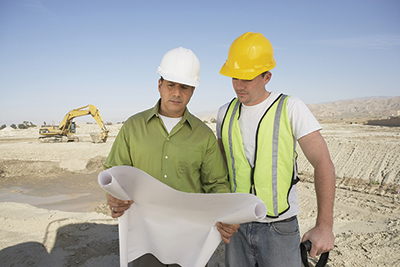
The first line of defense is the owner, since he establishes the criteria for success by picking a completion date. All too often, owners announce completion dates for projects before major design decisions are made and without the benefit of a meaningful, well-developed schedule. At this early stage, the plan should include preconstruction activities (e.g., land and right of way acquisition, environmental planning and approval, permitting, design, bid and award).
To develop a meaningful construction schedule, design should ideally be advanced to at least the 30-percent level; this is not always possible, however. When a milestone has to be established before design is sufficiently advanced, the owner needs to develop as detailed a plan as possible. The construction schedule should be built on a logical sequencing of work with production-based durations, proper allowance for weather and time constraints, impacts on operating systems, etc. The time and money spent on preparing a sensible, complete schedule avoids many problems.
Realistic Milestones with Contingencies
To establish realistic milestones, it is necessary to provide sufficient contingency commensurate with the degree of uncertainty. Conducting a probabilistic risk assessment involving all the stakeholders, and documenting the findings in a risk register can assist with this balance. Another way to establish contingency is to encourage the contractor to provide an early completion schedule.
Schedule Excellence
No matter how well thought out a milestone is, outside entities are needed to make it a reality. The vendor contract presents an opportunity to specify the behavior most likely to achieve success.
Often, the start of construction is delayed by problems with preconstruction activities. In this phase, delays happen because scheduling is not often a mandated process. This can be minimized by incorporating aspects of more rigorous construction scheduling processes into consultant contracts, and then really enforcing them.
A first priority in construction contracts should be specifying that the contractor hire a professional scheduler who meets certain qualifications. Next, a mandated planning process should be outlined that requires the contractor’s scheduler to lead a workshop with his major subcontractors and the owner’s representative. Activity maximum durations should be identified along with level of detail and types of activities, including sufficient detail for testing and commissioning.
Additionally, the contractor should cost load the schedule to the payment application’s schedule of values. This improves success because it obligates CM field staff to verify actual dates and percentage complete at the schedule activity level as part of the monthly walkaround. On larger projects, resource loading at the crew or trade level should be specified so that delays caused by contractors who did not staff to their plan can be identified and the situation can be corrected.
Other recommended behaviors include requiring contractors to adjust durations to match production to date; mandating participation in collaborative workshops to mitigate delays; establishing early completion bonuses; and enforcing liquidated damages provisions.
Of course, if something is specified, then compliance must be enforced to reap the benefit. This involves training staff and vendors in these uncommon clauses and confirming what is expected.
Collaborative Solutions
Every month, the schedule should be reviewed to identify potential delays, and timely corrective action should be initiated. If planned production rates are not being achieved, the contractor should adjust future activity durations to match the actuals, or submit a plan for improving production. Meetings should be held with the contractor to establish agreed-upon measures that make up for any delays.
Document Lessons Learned
Project teams often heave a sigh of relief when substantial completion is achieved, but then fail to bring the same rigor to closeout as was brought to construction.
To avoid this scenario, the contractor should include activities for detailed closeout activities and continue to update them.
Weekly meetings should also be held to push for on-time work completion. Lessons learned from things that went wrong should be documented and published so the team planning the next similar project can avoid the same mistakes.