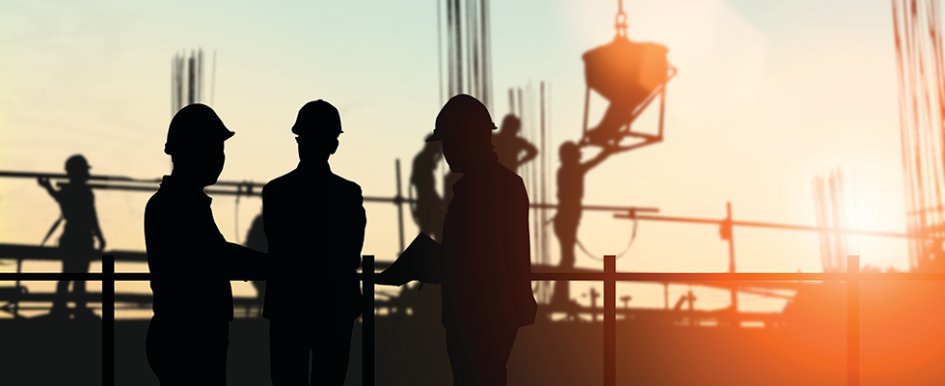
All construction projects carry some level of risk that needs to be identified, assessed and managed so construction projects are not negatively impacted. There are four main types of risk in construction: financial, safety, scheduling and legal. Effective risk management helps construction companies grow profits by ensuring projects are completed on time, within budget and without incident.
By following these steps, construction companies can minimize the impact of potential risks and hazards on the project, ultimately ensuring the successful completion of the project:
- Risk identification
- Risk assessment
- Risk prioritization
- Risk mitigation
- Risk monitoring and control
Identifying Risk
Risks associated with a construction project need to be identified. These include environmental hazards, design flaws or construction site accidents. It’s important to note that risk identification should be an ongoing process throughout the construction project, as new risks may arise as the project progresses.
To identify risks, project plans and specifications must be reviewed to uncover design flaws, site constraints and regulatory compliance issues. Site inspections should be conducted with management looking at issues with site conditions, environmental hazards or safety concerns. Project stakeholders, such as owners, engineers and contractors, should be consulted to alert the project lead if there are any budget constraints, changes of scope or scheduling issues. Brainstorming sessions with project members can uncover potential risks that have not been previously considered.
Project teams can review historical data from similar construction projects to help identify potential risks that may have been encountered in the past, such as delays, cost overruns or quality issues. With a risk checklist, managers can systematically review all aspects of the construction project for any additional risks. Identifying risks early in the project allows project teams to be more proactive instead of reactive, helping save time and money.
Assessing & Prioritizing Risk
Once the risks have been identified, construction businesses need to analyze the identified risks to determine the potential impact the risks will have on your project. Prioritize the risks according to the potential impact so you can act on the most threatening risks first. Assess the likelihood that each risk will occur and its potential impact on the project. This evaluation can be done using a risk matrix or a similar tool to assign a likelihood and impact score to each risk. By prioritizing risks on potential impact, project teams can focus their efforts on the most critical risks that require immediate attention.
Then you will need to develop strategies to minimize the impact of the risks. These strategies can include redesigning the project, changing the construction methods or materials, implementing safety measures or developing contingency plans. Construction firms can optimize the project design to minimize potential risks by using more durable materials, minimizing construction site hazards or improving the project’s functionality.
Safety measures should be implemented to reduce the likelihood of accidents and injuries, such as using protective equipment, establishing safety protocols and training workers on proper safety procedures. Develop contingency plans that outline a course of action for unexpected risks or issues, such as developing alternative project plans, establishing backup suppliers or having a reserve budget.
Team members should be chosen to implement these mitigation strategies. Most importantly, resources such as time, money and personnel must be allocated to implement the strategies effectively. Hold regular project meetings to maintain open communication and collaboration between the team members to ensure risk mitigation strategies are being implemented smoothly and promptly.
Using comprehensive skills and certifications management software reduces risk. With these tools, you are confident that you are sending the right person to the right job and that the crews have the right skills to do the job. This software keeps crew certificates up to date, so your business is not exposed to a regulatory fine.
Mitigating Risk & Managing Projects
Risk mitigation at your construction project can be improved by using technology, such as project management systems that automate the tedious tasks of project management so managers can spend more time making profit-impacting decisions. With daily job costing and progress tracking, project managers can know which projects are profitable and on time without setting foot on the jobsite so they can focus on the projects that need intervention.
With project management technology, project managers can regularly review the project’s progress to ensure the project is on time and on track. You can identify potential risks that may arise due to delays or changes in project scope; then, you can evaluate whether your risk mitigation strategies have been implemented and are effective.
Contractors should document all risk management activities to mitigate risks adequately. Communicate regularly with project stakeholders, including the project owner, contractors and other team members, to ensure that everyone is aware of any changes in the risks and the status of the risk mitigation strategies.
Monitoring & Controlling Risk
Continuously monitor and review the risk assessment throughout the construction project to ensure that risks are being effectively managed and that new risks are being identified and addressed as they arise. Implement quality control measures to ensure the project meets the required quality standards and specifications, such as establishing quality checks, conducting regular inspections and hiring qualified professionals.
A well-planned project is less likely to experience unforeseen risks. Develop a comprehensive project plan that includes timelines, budgets and risk assessment. The risk assessment should cover site conditions, construction methods, materials and environmental factors. When monitoring risk, focus on quality control by including inspections, testing materials and workmanship to ensure compliance with specifications and industry standards.
A comprehensive safety management program can minimize risk on the jobsite, including reducing the chance of accidents and injuries. A safety management solution eliminates paper in processes so that all project team members can see what is happening and what needs to be done to ensure a safe jobsite.
The software can help identify and evaluate potential hazards on the jobsite, such as documenting unsafe work practices, environmental hazards or hazardous materials. Implementing a safety management solution ensures that the project complies with local, state and federal regulations. The software collects safety records and documents that can be shared with regulators. It will report and track incidents and near-misses and allows the project team to review data to identify trends and patterns that can help prevent future incidents.
Safety management software allows foremen to electronically record safety meetings and easily keep track of attendee signatures and photos. Users have access to more than 1,000 built-in safety meetings and have a history of all previous safety meetings at their fingertips for easy access. By ensuring that all stakeholders on the project are aware of the risks and how to address them, the risk of accidents and injuries. is reduced.
Effective risk management is critical to the success of construction projects by helping to avoid project delays and cost overruns and enhancing safety and improving quality, resulting in improved profits and customer satisfaction.