Each year in the United States alone, more than 200 construction workers are killed by falls and more than 10,000 are seriously injured. According to the Occupational Safety and Health Administration (OSHA), falls are the number one cause of death in the industry, accounting for more than 36 percent of all deaths in 2013. By ensuring workers are properly trained, companies may be able to avoid the physical, emotional and financial distress that often results from an accidental fall.
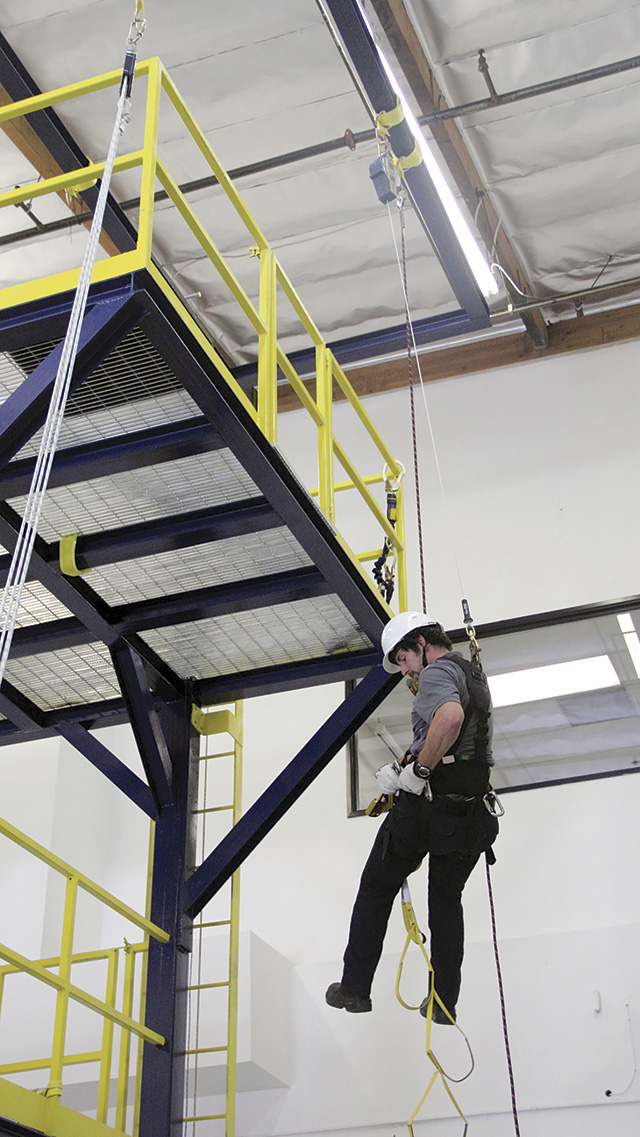
Fall Protection Saves Lives
In addition to the loss of life, fatalities from falls can easily bankrupt a business. This can be true even if the worker survives the fall but is seriously injured, as long-term injury care and wage loss can cost as much as a death settlement.
In fact, more than $40 billion in workers' compensation benefits is paid each year by employers and their insurers. That is nearly $500 per covered employee, according to the American Society of Safety Engineers (ASSE). According to OSHA, businesses spend $170 billion a year on costs associated with occupational injuries and illnesses—expenditures that come from the company.
A company could also face fines for violations from OSHA, which can often amount to hundreds of thousands of dollars. If OSHA deems that the violation was a direct result of refusal to provide proper equipment, it may be considered a criminal conviction and include jail time. Without proper training, workers may not realize the severe consequences of a fall, which include serious injury and death.
The Right Training
Falls can be prevented when workers understand how to properly set up and use their fall protection equipment.
Training should provide in-depth sessions on regulations, potential hazards, equipment selection and instruction on how to use the equipment correctly. Hands-on training should be provided throughout every step of the process.
The most effective training programs mimic actual work conditions so workers can apply what they've learned to real situations. By giving participants the opportunity to handle fall protection equipment, they can learn firsthand what components should be inspected before each use.
Supplementing and combining hands-on training with classroom instruction like this is invaluable because it helps workers apply what they learn to real-life situations.
To ensure the training meets the above requirements, the training should be provided by a "Competent Person Trainer," as set out in ANSI Z359.2. If the instructor meets the ANSI standard, the employer can rest assured that the training meets the minimum requirements for a comprehensive program that also complies with the OSHA regulations.
On-Site vs. Off-Site Training
On-site safety courses take place on the jobsite and allow participants to apply the training directly to their specific daily work activities. By training in and around the workers' normal environment, employers can help to make safety training immediately applicable to their employees. Off-site courses take place in a controlled environment at a facility that is designed to offer practical experience in situations common to the industry.
On-site safety courses force instructors to modify the training based on the available space, its structures and its apparatuses, but they also save travel costs and time for company employees and allow the company to tailor course content.
Off-site courses, on the other hand, are open enrollment and draw a wide variety of safety professionals from different backgrounds. As a result, they often facilitate dialogue among participants that allows them to share best practices and learn from their peers at other organizations. Off-site training sessions may also give attendees an opportunity to visit the company's manufacturing facility and test lab, where fall protection equipment is manufactured and assessed through a series of tests for quality assurance purposes. Many fall protection equipment manufacturers offer both on-site and off-site training.
Training Selection
There are several respected, dedicated training companies operating in the U.S. that can offer customers meaningful fall protection training. However, it is important to remember that there are no governing laws that regulate who can become a trainer. Here are a few considerations to keep in mind:
- No matter what type of training a company chooses, it should make sure that a reputable instructor or company teaches the course and that hands-on learning is a central part.
- Be wary of one-day training courses that promise to cover it all for less. Also, steer clear of off-site training courses that take place in a conference room or hotel meeting room. Look for training courses that include modules in rescue and dropped objects prevention, as these are both important components of fall protection that are sometimes overlooked.
- Check to see whether the training literature or website says the training meets OSHA, ANSI or other relevant standards.
- Investigate whether the company has more than one training facility and if it has fall protection gear available for all students to use, handle and inspect during each class.
- Ask whether the company employs full-time trainers and whether these trainers have relevant experience in fall protection.
At the end of training, employees should confidently be able to answer the following questions:
- What are the potential fall hazards?
- Which equipment is best for the job?
- Where is that equipment located?
- What is the correct way to wear equipment?
- What happens in the event of a fall?
- Is my equipment in good working condition?
To meet ANSI standards, there are a few key courses that have requirements for refresher training periodically. Check to ensure your training provider offers refresher training for those courses, too.
Fall Protection Investments
It is important to treat a strong fall protection program and a prominent safety culture as a solid business investment, rather than as an expense.
By investing in safety training, companies can avoid serious injuries and save lives, increase performance in areas that impact insurance modification ratings and improve working conditions. OSHA studies indicate for every $1 invested in effective safety programs, companies can save $4 to $6 as illnesses, injuries and fatalities decline.
The ASSE reports that a fall protection program implemented by a U.S. construction company reduced their accident costs by 96 percent, from $4.25 to $0.18 per person, per hour. In the end, a solid fall protection training program is a sound business investment—not just another expense.