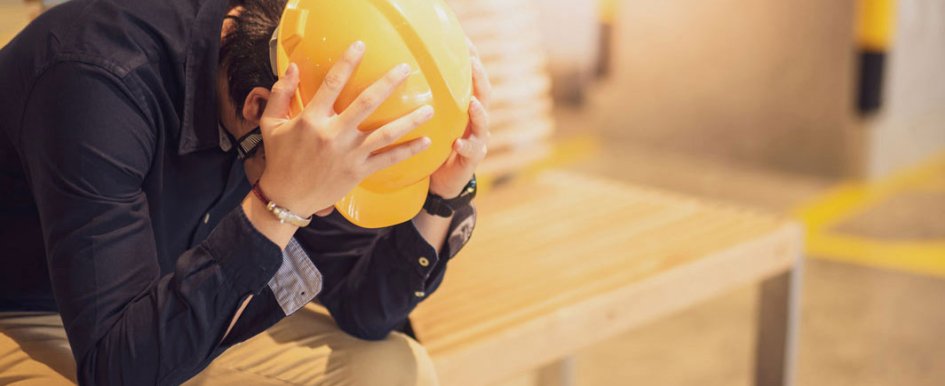
In 2012, Navigant Construction Forum of Navigant Consulting Inc. reviewed 15 studies—homing in on 19 projects discussed in those studies—to quantify the true price of rework in construction. The report defines rework as “activities that have to be done more than once in the field, or activities which remove work previously installed as part of the project—regardless of source—where no change order has been issued and no change of scope has been identified by the owner.”
The responses of contractors interviewed in the studies allowed researchers to peg the direct cost of rework at almost 6 percent of the total contract amount, with indirect costs of 5.5 percent. Fortunately, contractors have a good chance of improving profitability by reducing or eliminating rework. But these tasks don’t come without their challenges.
The first seeds of rework typically hide in your construction processes. Incomplete or delayed requests for proposal leave people working without the right information or specifications; inadequate resources encourage people to cut corners; poor scheduling ensures work sequencing gets out of whack; poor design and engineering not only raise safety concerns, but also guarantee people will be making changes on the fly.
Rework points to systemic issues, given that it arises from the systems or processes you use daily. But it’s not just your problem. Much of what flows (or doesn’t flow) into your systems comes from other project participants. Subcontractors, suppliers, fabrication producers and others who supply materials, components and resources leave you at the mercy of everything they do incorrectly. To truly tame rework, you have to start at the beginning.
1. Start with Scope
The project scope provides the first glimpse at the potential for rework. If you’re looking at plans and scratching your head to understand how the pieces fit together, you have just been warned of possible changes. And changes spawn rework. The following tips can help you focus on the important factors when analyzing the scope of a project:
- Use a documented, consistent approach when studying plans.
- Confirm existing conditions.
- Compare the plans to the stated scope and intended use.
- Compare the plans to similar projects you have already built.
- Compare plan specifications with plan sections.
- Consider the expected completion date relative to the workload.
Carefully review the contract and look for vague or missing requirements. Use the review to inform not only your bid, but also your decision about whether to bid at all. After winning the job, focus on scheduling.
2. Analyze the Schedule
As construction gets underway, a false sense of security leads us to believe all parties know what’s going on and what their respective roles are. This is seldom the case, though. Wishful thinking will lead you to overlook the warning signs that rework is brewing.
Take a good look at the schedule—not just a cursory review, but a thoughtful, in-depth study. Identify the activities that might be lacking sufficient resources. Those tasks are where substitutions, improper methods and rushing will spin off quality issues.
Look for instances where activities are out of sequence or not well planned or thought out. The biggest variable here is time. Time passes; things change; and change is the precursor to rework. So, watch your schedule like a hawk and move quickly to get ahead of the rework causes as soon as you spot them.
3. Enforce Specifications
You often encounter rework issues as a result of others’ subpar work. Material substitutions and inappropriate methods creep into the project from all corners. If subcontractors decide not to ask for clarification on how to install a component, or off-site fabricators substitute one material for another, you end up owning the problems.
To help avoid this ownership of error, be sure to qualify all of your project partners, and make sure all documentation is easy to view and always up to date.
Regular checks on work in progress can also reveal issues that might create rework. Referencing your schedule, observe and review the activities in which you noted rework could blossom, making sure workers are using the right materials and methods.
4. Formalize Quality Control
If you don’t have a formal quality control process, you will inevitably face rework. “Formal” doesn’t have to mean complicated. A simple documented process works just fine for many project types and sizes.
With your quality control process in place, the next aspect is training. Beauty is in the eye of the beholder, and there is a lot of latitude in the phrase “acceptable workmanship.” This means you must train your employees to understand the difference between “good enough” and “meets quality standards” at your company. Likewise, you and the client must take the time to agree on what constitutes quality.
Then, it’s very important to make sure the same is conveyed to your quality control leaders, which includes supervisors, project managers and any others in a position of managing certain project components.
As today’s projects include increasing amounts of high-tech components, you also have to manage more third-party inspections and verifications. Make these items easily visible on your schedule and allot time for reminders and for confirming technical aspects with installers.
5. Analyze & Document
You can actually avoid rework by tracking rework—this could be as simple as attaching notes to the schedule wherever rework crops up. When you collect those notes at project’s end, you can use them to improve your rework assessments on future similar projects.
Another benefit to tracking rework is studying the trends. Over time, you might notice a certain subcontractor has many small rework issues that never amount to a big deal but foretell bigger problems. Or you might discover shop drawings from a certain supplier often fail to specify materials that exactly match the plans.
These all point to systemic lapses in reporting and are the kinds of rework precursors that go undetected until it’s too late. Analyzing rework after the fact is a sure way to head it off in the future.