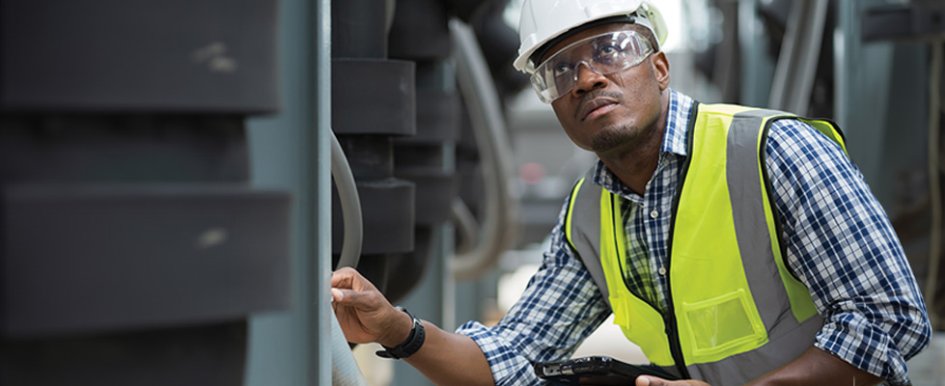
In a world where the only constant is change, the construction sector is catching the digital wave, transforming its foundational bricks and mortar into pixels and data.
This revolution isn’t just about keeping pace; it’s about setting the pace, leveraging the power of computerized maintenance management systems (CMMS) and computer-aided facilities management (CAFM) to forge a future where efficiency and innovation become the backbones of the industry. For owners of construction businesses, efficiency and innovation are not merely industry buzzwords: They can translate to a very positive impact on the bottom line.
As we peel back the layers of this digital revolution, it becomes evident that CMMS and CAFM are catalysts for change, empowering companies to navigate the rough waters of economic uncertainty, soaring operational costs and the relentless pursuit of efficiency. What’s more, these tools can be used to optimize virtually every process and procedure under a company’s roof — including asset and facility maintenance, two areas of a company’s operation that don’t get the attention they deserve.
Gone are the days when maintenance was a mere checkbox on the daily to-do list. Today, by leveraging CMMS and CAFM technologies, companies can fundamentally transform their maintenance function. The maintenance landscape is being remodeled, creating a future in which every nut, bolt and screw is a part of a well-oiled machine.
Digitizing maintenance through CMMS and CAFM solutions positively impacts the maintenance workforce. Companies are managing key assets differently to improve their operational and production effectiveness, and it’s delivering significant financial benefits.
Pressure to Maintain, Not Replace, Equipment
Most organizations are facing economic instability, rising operational costs and increased material prices — all of which affect profitability. In this climate, organizations are looking for ways to reduce costs and increase efficiency. This improvement drive is pressuring maintenance teams to optimize asset performance and availability.
Most businesses prefer to defer equipment replacement until more profitable — and more predictable — times. As a result, maintenance teams are given the unenviable task of prolonging the life span of existing assets, which means ensuring those assets and their infrastructure are entirely reliable. In these scenarios, CMMS software plays a critical role.
When an asset breaks down, it could have a cascading effect on the entire operation. Planning when to regularly check and/or maintain a piece of equipment will prolong its life span, as maintenance teams can spot issues before they occur. Monthly checks, quarterly maintenance and annual overhauls are reducing failures, increasing machine efficiency, improving productivity and enhancing the effectiveness of maintenance teams.
Of course, managing these programs is complex work. That’s why forward-thinking companies have moved away from using a calendar or spreadsheet to plan preventive maintenance schedules. In their place, they use digital CMMS platforms to manage their maintenance teams and regularly check assets.
Fewer Skilled Workers = More Machines
By 2030, the global manufacturing industry is expected to experience a deficit of more than 7.9 million people.
In the U.S., the manufacturing skills gap could result in 2.1 million unfilled jobs by 2030; the cost of those missing jobs could potentially total $1 trillion in 2030 alone, according to Deloitte. Which all goes to say that finding skilled people is currently a gargantuan challenge for many companies.
How does this all relate to asset and machine maintenance? With talented people in short supply, many companies are automating processes to drive production with reduced head count. But more machinery increases the workload of maintenance teams
In light of a greater digital investment, operational leaders are looking for ways to better monitor and manage underprioritized areas such as asset maintenance. Industry leaders are now using CMMS systems with business intelligence tools such as Microsoft Power BI to combine data from their maintenance systems with information from other production systems. This integrated approach allows them to monitor the effectiveness of production lines.
CMMS software is also giving maintenance teams greater insight into their workforce, monitoring the effectiveness of shift teams week by week. Gathering this type of data will allow companies to further reduce skills and efficiency gaps, and ensure they are retaining the right employee levels in their maintenance operations.
Improving Maintenance, Improving Sustainability
While profitability is a priority in the current fluctuating market, it’s not the only target. Many companies are also focused on reducing their environmental impact. And maintenance plays an important role in helping firms lower their carbon footprint.
Streamlined asset and facility maintenance enables companies to identify inefficiencies and other technical issues more quickly. In fact, CMMS software solutions can empower maintenance teams to:
- Regularly monitor meter readings to understand and optimize energy consumption.
- Monitor waste for production line shifts.
- Reduce/remove paper-based systems such as permits and risk assessments.
- Closely manage maintenance team visits to reduce mileage, fuel use and emissions.
- Improve machine maintenance to reduce production downtime and maximize energy efficiency.
- Increase the life span of equipment to reduce wastage/scrappage.
- Manage stock movements and purchasing to optimize availability and reduce transportation emissions. Implementing CMMS software as part of an overall digital transformation strategy also helps unite operational technology (OT) and information technology (IT). Well-integrated solutions improve data visibility, which enhances sustainable decision-making.
Linking IT & OT
The relationship between IT and OT for data collection and analytics has been well established. But there are other ways IT can help companies improve asset maintenance. For example, the transfer of data and controls between a CMMS system and an enterprise resource planning (ERP) system helps businesses manage stock and purchasing processes without manual intervention or double-keying entries.
CMMS software can also use data from other digital assets to operate more efficiently. Many CMMS users claim that linking IT and OT systems using API technologies improves metrics and process automation. With such connectivity in place, maintenance becomes a value-driving area rather than an expense — music to any business owner’s ears. Operational teams can demonstrate and report on how CMMS software boosts efficiency, streamlines processes and reduces waste.
Market conditions and company goals have turned asset maintenance into much more than a routine process. Today, companies can digitally transform their operations to influence how well they run and grow their profits. And operational teams can now be accountable to upper management, shareholders and customers.
Though changing asset and facility maintenance from expenses to money generators seems like a magic trick, it’s anything but. It’s the result of applying the most current CMMS and CAFM technology to these areas. Even organizations with well-established plans are taking a fresh look at asset maintenance in 2024. Modern systems and processes can help them overcome economic pressures and future-proof their business.