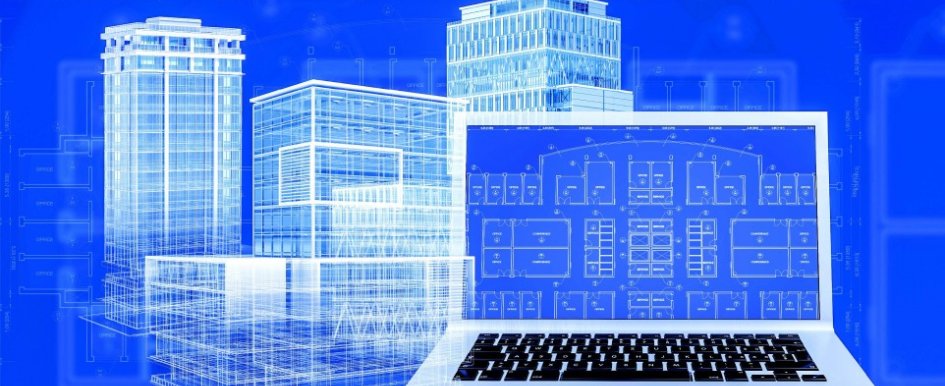
What a difference 10 years can make in the world of technology. That's how long it has been since 3-D modeling began infiltrating the construction business. Building information modeling (BIM) has evolved from simply being a way for design architects to communicate their vision to clients to becoming a means to building better structures. Recent advances in 3-D modeling technology acknowledge the value to the construction industry of working from an accurate buildable model throughout the entire construction process. Construction companies will continue to use 3-D models in new ways to improve their internal processes and competitive posture, and they will adopt the new technologies that will soon hit the market to further improve performance both in the office and at the jobsite.
True Constructible Models
Architects were the first to embrace 3-D modeling to communicate their designs, but these types of models are of little value to general contractors, other than to see what the finished structure should look like. That doesn't imply that 3-D modeling is useless to the construction process, though. There is a distinction between 3-D models built to communicate design intent and those built for construction. Constructable models include all the details general contractors and subcontractors need to build a structure to meet the design intent. This high level of detail allows any kinks to be worked out well before the first excavator rolls onto the jobsite.
General contractors who require subcontractors to produce, use and share constructable models find that the models aid in planning, coordination, communication and construction by supplying the detailed project information needed to build a structure. In addition to improving construction company processes and efficiency, information contained in the model can generate accurate cost and material estimates, produce coordinated schedules, drive steel fabrication and produce erection sequencing plans. The trend is for general contractors to require constructable models for projects of all sizes and complexity to improve collaboration, planning and logistics with subcontractors, architects, engineers and project owners.
Beyond 3-D to 4-D and 5-D Models
There is a growing trend to adding time (4-D) and costs (5-D) to a constructable model to extend its use into scheduling and estimating for planning and construction. The level of detail present in a constructable model enables highly accurate quantity takeoffs, which drives better cost estimation. Likewise, applying dates to pieces in the detailed model provides a visual way to see the construction schedule at a very granular work package level. This helps general contractors and subcontractors to estimate the cost of the project and provides a workable schedule that can be used to coordinate the trades and keep the project on track.
Construction Safety
Safety is the biggest priority of any building project. The need to build successfully and safely is the reason why details and information are necessary beginning in the design phase. While Chicago-based concrete construction company Adjustable Forms has modeled safety systems into its concrete models for years with the tools at hand, incorporating safety functions into 3-D modeling tools has lagged behind other features. However, the potential to use technology to improve safety is promising. Georgia Tech is in the process of developing advanced tools for analyzing a 3-D model to assess and suggest safety measures. For example, if penetrations in slabs are large, the software automatically generates barriers around it; any exposed edge of a slab above ground level will equally receive a barrier. This is a good example of how 3-D modeling will be used in the future to improve safety.
Robotic Total Stations
While it is typical to drive robotic total stations from 2-D drawings, there is a growing trend to drive them from information contained in a 3-D model. Concrete contractors who use robotic total stations to lay out points at the jobsite can take direct feeds from the model, which results in dramatic productivity improvements. The Weitz Company, a general contractor and construction manager located in Des Moines, recently laid out over 500 points, including sleeves and anchors, on a 15,000-square-foot deck in a single day by taking information directly from the model to the robotic total station.
To ensure quality control, some general contractors are taking as-built information from the field and putting it back into the model to compare what has been built with the plan to ensure accuracy. This can be done by capturing as-built locations using the robotic total station and importing those points into the BIM model to check for positions that deviate from the design. Alternatively, it's possible to take a laser scan and overlay the point cloud over the BIM model for a visual comparison and long-term, as-built record.
Information Accessibility
Another growing trend with 3-D modeling is empowering all project team members by giving them direct access to the same set of up-to-date information, whether they're in the office or in the field. Viewing a model on a mobile device allows everyone working on the project to use the model to better understand his or her portion of the job. Tech savvy or not, everyone on the construction team can benefit from 3-D without being a BIM guru. Because the mobile device will always display the latest version of the project model, there will be no question about whether the field crew is following the right plan. Beyond the benefit of the greater understanding that visualization brings, mobile-device, model-viewing tools can also be used for checking dimensions and pulling quantities from the model.
Augmented Reality
Wearable technology is a hot topic for personal health and fitness and virtual reality gaming, but it is currently moving beyond consumers and into business. Microsoft and Trimble Buildings have partnered to adapt Microsoft HoloLens, wearable holographic technology, to the A/E/C industry. The collaboration will extend interaction with 3-D models beyond the confines of a 2-D computer screen, creating new ways for the many stakeholders of complex, multi-phase construction projects to visualize, collaborate, share ideas and manage change. This includes enabling remote teams to review and more effectively collaborate to resolve constructability issues in real time.
Use of Drones
It may not be long before using drones to photograph and video a building site or visually appraise construction progress will become a common practice for general contractors in charge of large, complex projects. While using drones to photograph building sites and evaluate progress does not directly relate to 3-D modeling yet, it has an advantage to the construction process overall.
The use of 3-D models in construction is evolving in exciting ways that will continue to improve the way projects are planned, coordinated and built. These technological advances will help general contractors build better structures with more accuracy, quality control, safety and efficiency. Many of these technologies are already in use and others will be commercially available soon.