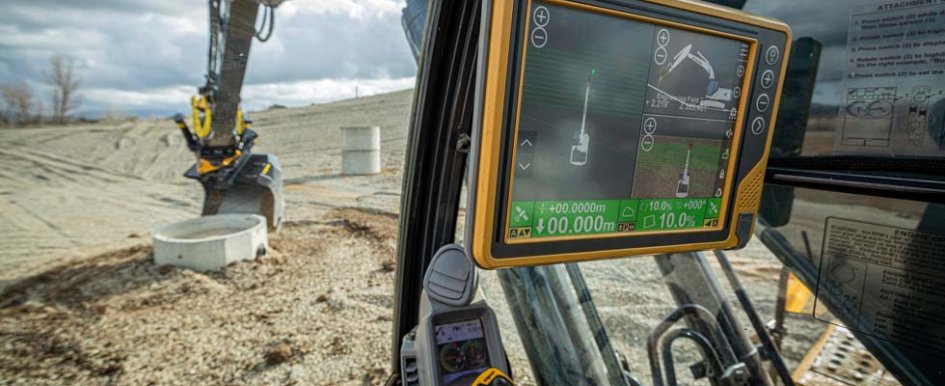
From excavators that can automatically dig to depth, to trucks that drive themselves, machine control technology is revolutionizing the construction industry. Machine control hardware and software solutions were developed to determine a machine’s current position on the earth and compare it with the desired design surface.
Using data from satellites or total stations and 3D models, the technology ensures that machine operators can accurately position machinery, check grade, automate equipment functions and collect data. Using various positioning sensors and a display, machine control systems provide operators a clear reference between the position of the machine bucket or blade and the design surface.
Used by the construction industry on earthmoving equipment since the late 1990s, the technology allows decisions to be made based on data, rather than relying on the skill of the operator. As a result, machine control solutions on dozers and graders save operators time, money and fuel.
The Skills Gap
The construction industry of today faces many challenges. It is no secret that there is a lack of fresh talent entering the sector and many seasoned operators have reached retirement age or have moved on to other careers. The industry has had trouble attracting younger people as well and as a result, there are fewer operators entering the profession.
Should this trend continue, the industry will be left with a shortage of experienced operators, which means that the quality and productivity of projects will be impacted by a significant skills gap. To meet targets and tackle the skills gap head-on, the industry is turning toward automated machine control to improve workflows.
Automated Machine Control
Going beyond simply providing operators with a visual guide to bucket or blade position, automated machine control moves the blade to grade by communicating with the machine’s hydraulics. Unlike regular machine control, automated machine control technology places the responsibility for accuracy and speed firmly in the hands of performance-enhancing technology. This means that using this technology, new or less-skilled operators can perform like a professional and even the most experienced operators can work better and faster.
Tech Adoption
With the demands for productivity increasing and a shortage of skilled operators, construction business owners should consider the benefits that investing in automated machine control can bring to their company. There is an opportunity for the industry to transform construction workflows by investing in automated excavation systems, taking the first step toward a fully automated jobsite. For example, some manufacturers today provide options that use the same components of the original machine control system with the addition of an ultra-smooth hydraulic interface.
With easy-to-use finger-tip control, the technology is designed to provide automated depth control when digging to grade in flat, stepped or sloped applications. The system allows experienced operators to work better and faster, while new operators can perform like a professional.
New machines using machine control technology allow operators to automatically control digging depth, boom elevation and the bucket angle — ensuring that they are on-grade every time. This saves both new and experienced operators time and money, through an estimated increase in productivity of around 30%. The technology also means that operators only move the earth that is required, which in turn avoids over-digging — saving additional costs of fuel and unnecessary transportation of materials and rework.
Automated 3D machine control systems also provide onsite safety benefits. By using the most advanced and precise GPS positioning technology and sensors, operators receive real-time, dynamic, on-screen bucket location and design views. Access to real-time designs means that operators can cut more accurately and check against complex designs in the cab.
Thanks to onboard connectivity, automated machine control systems like these can also be used alongside software to give teams remote access to the excavators while generating can from each machine and communicated to a central point. Reports, data and even designs can be shared between the office and the in-cab display to ensure operators are being updated when changes are made in real time — reducing the need for rework if plans change.
The Future of Automated Machine Control
Automation is just the first step for machine control. Looking forward, not only will automation control machine angle and depth, but the whole excavation process is likely to become automated — increasing productivity across the entire construction workflow.
Using automated machine control technology, machines will be able to act as sensors — monitoring the progress of projects and sharing accurate reports on productivity. For the wider construction workflow, these reports will then be used to synchronize with other functions and equipment — such as trucks — to further streamline processes and avoid unnecessary downtime.
In the future, fully automated construction workflows will allow project managers to accurately assess the rate of progress and resource the operation appropriately. Business owners should ensure that they are upskilling their workforce through this technology and embracing the benefits it brings to projects as fully automated construction workflows continue to be utilized to address future infrastructure targets.