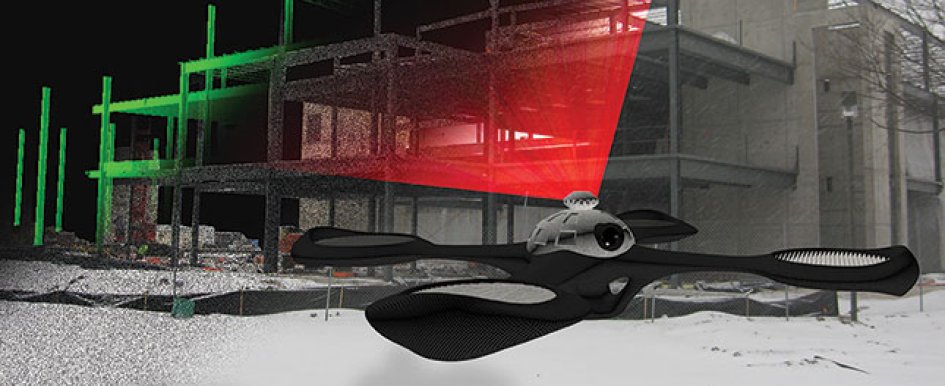
As a design and construction professional with more than 30 years of industry experience, I am shocked that construction is still an inefficient business. Multiple sources have documented that overall productivity in the construction industry has decreased throughout the last few decades. Despite all the tools and electronics on jobsites today, data from the U.S. Department of Commerce and the Bureau of Labor Statistics show that the industry is less productive than it was in the 1960s. Why? Many firms are still using multiple documentation and management processes that are 50 years old or more. Paper prints and specifications are still the major documentation tool. To complicate the problem, as our projects have become more complex, we have added more documentation, duplicated tasks and delegated responsibilities, creating a huge volume of waste. With all of this waste, we are forced to be less productive.
Below are a few examples of current issues construction firms face.
- Today, a structural engineer produces structural drawings as bid documents. After the bid, the steel fabricator redraws these sketches for fabrication. He then develops detailed drawings for the connection and installation of the components. These drawings—which are, in most cases, still paper—are shipped back to the general contractor who reviews and sends them to the engineer. The engineer then reviews them, marks them up and sends them back through the process to start over again.
- A common assumption is that contractors make the majority of their money from change orders. However, change orders are one of the most inefficient processes during construction. For example, imagine that a contractor observes a duct that will not fit above the ceiling, so he prepares a request for information (RFI). He must prepare the RFI, create a drawing to show the condition and then ship both items to the design professional. The design professional then has to review the RFI and prepare a response. If the response adds cost to the project, the contractor must prepare a change order. This requires more documentation and more time from staff. The change order then goes to the design team for review and possible challenge. In the meantime, the field has to stop work, move to a different location and wait. After multiple reviews of this issue are completed, the issue goes to the owner with more paper, more documentation and more time.
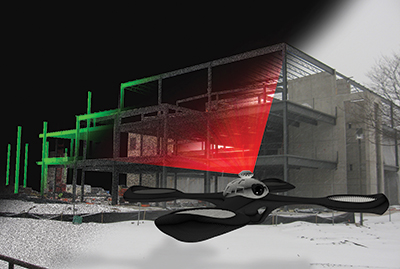
Do you see any inefficiencies in these two processes? Now, think about all the other duplications and documentations in construction: pay application process, the entire project documentation process, shop drawings, the lack of sharing of documents between participants—all adding more inefficiency to the process.
This is the world we live in: Everyone wants documentation of every decision and delegation of responsibility to avoid liability. Some things will not change. The good news is that the future offers the industry opportunities to
improve these inefficiencies and build stronger businesses.
BIM for Better Workflow
Building information modeling (BIM) is in its infancy with respect to its potential for improving the industry. Part of this improvement must be based on a BIM process that includes all stakeholders, from design to operations.
Today, disclaimers are circulating that warn about allowing anyone other than the designer to use BIM. However, we need to break this paradigm. A BIM process that starts with the design team and flows to the contractors, subcontractors and then the owner’s operations team is the key to success. Below are some examples of how this model can improve today’s processes.
- A structural engineer prepares his structural design in a BIM interface. The BIM model is handed over to the structural detailer, who uses the structural BIM to add connection details. Because this is one model shared through the cloud, the structural designer can review the connections as they are added. The structural model then flows to the fabrication floor, where the structural steel is cut and marked based on the BIM model. Since the model can have an embedded schedule, the trucks can be loaded and pieces marked with QR codes for sequential installation. This method improves the flow of shop drawings, fabrication, delivery sequence to the site and speed of installation.
- Similarly, the sharing of a BIM model with the entire construction team means that clash of a duct with a pipe never gets to the point of a change order. The conflict is detected in a 3-D world long before it gets to the field. Not only does a fully coordinated model reduce the change process, but it also allows the trades to work on prefabrication and panelization of components. The BIM model can be used to coordinate the construction sequence and installation, making real prefabrication a possibility.
Once the industry masters the art of sharing the entire BIM process among all stakeholders on a project, construction firms can begin to capitalize on even more opportunities that are shaping the future.
Robotics on the Jobsite
The expansion of robotics on the jobsite will provide a dramatic opportunity for contractors to improve their workflows. Robotics are beginning to connect to BIM models and travel along floors completing wall layout. Although still a prototype, this is a small sampling of what robots can do.
Future robotic applications on jobsites will include lifting and placing of prefabricated components and even the installation of metal studs and structural steel with quality welds coordinated with BIM. These robotic capabilities, combined with the development of quadcopters and drones, could further transform theindustry, allowing robotic machines to fly materials to the site and deliver them to the specific location indicated by BIM.
Laser Scanning and Quadcopters
The addition of sophisticated quadcopters that can be programmed to read a BIM model adds a new layer of technology. Quadcopters can fly through a building on a daily basis utilizing a laser scan capability. The laser scan can be used to compare and document the progress from the previous day’s scan, and the scan can be compared to the BIM model to verify that all components are installed in the correct locations. With the development of object recognition, the scan also can verify that the correct components have been installed. So, now, a quadcopter with a laser scanner can do quality assurance and feed data for the pay application on a daily basis. In addition, robotics can work 24 hours a day, seven days a week, allowing for a huge jump in productivity.
3-D Printing
Today, a small desktop 3-D printer can cost less than $3,000. In most cases, these are novelty items for printing small models or trinkets. But, the potential of 3-D printing is limitless. The University of Southern California is now prototyping 3-D printing of full-height concrete walls. This process reads the wall layout from a BIM model, requiring no formwork and no stripping of forms. Plus, the process works regardless of the shape of the wall. Imagine 3-D printing of countertops, exterior enclosure components and even door hardware.
3-D printing could dramatically minimize shipping of bulk materials to the site and reduce on-site storage, because materials are printed as needed. Future jobsites could have on-site 3-D printing stations that could reduce material waste handling. With materials printed as needed, no packaging or shipping crates would be required, and businesses could save huge amounts of fuel that would otherwise be consumed when moving materials to the site. This technology could result in combined savings in every step of the process.
Looking Toward the Future
With the implementation of all this technology, what will happen to tradesmen? Even with all of these technologies, construction jobs will require just as many tradespeople.
The difference is that the skill sets of these individuals will be dramatically different, having more to do with programing, robotics management and data management. The industry will still need skilled tradesmen to complete the work, but their skill sets will be more technology-based.
If we improve the jobsite and make it more efficient with robotics and quadcopters, what will happen to the business aspect of the construction process?
If firms can fully integrate with BIM, the efficiency of business operations will improve. BIM will become the source of truth for contractors. It will verify the quantities in bids from subcontractors, help solve problems through clash detection and coordination, and provide opportunities for prefabrication and modularization.
The daily laser scans will feed into an automated pay application process, and the quadcopter will fly through buildings, scanning the progress of construction and allowing information to be submitted to an automated pay application process. Payment to the contractor will become weekly or daily. The cash flow for the contractor will completely shift, and the profit margins will improve by simply improving cash flow.
Every piece of technology that has been described here exists today. These technological systems may not be fully developed, but all of these future applications are possible and have the ability to completely change the construction process.
In order for these technologies to transform the industry, we must maximize the full potential of BIM technology. We must figure out how to develop a complete BIM process that can flow to all stakeholders on a project—from the designer to the contractor to the facility operations team. When we can embrace the ability to share BIM, we can begin to break the pattern of waste and inefficiency in our industry.
Printing the Jobsite: 3-D Printing Technology Could Take Efficiency and Safety to a New Level
By James Benham
We may be far from walking up to a replicator like Picard did in Star Trek to order an “Earl Grey, hot,” but advancements in 3-D printing are proving that technology is on its way to making science fiction a reality.
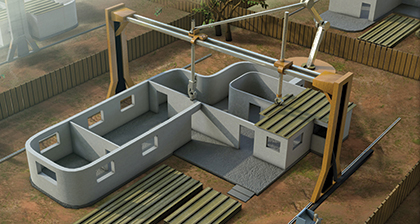
Whether it’s printing a spare screwdriver or an iPhone mount for a GoPro base, consumer products such as the Makerbot Replicator 2X give us the ability to create plastic objects from 3-D models on a small scale. On the next level, engineering, architecture and construction research consulting firms are experimenting with materials other than plastic that would be more useful to structural printing, such as steel, ceramics and even hardened resin. From steel nodes to one-bedroom concrete houses, 3-D printing is happening around the world and will continue to get better at building bigger—and more safely.
The ultimate vision for commercial construction, as I see it, is a combination of several of the most advanced technologies in development, with 3-D printing being the final step. Starting with something as simple as a tablet, contractors will visit a jobsite and use a 3-D laser scanner to map the existing structure or environment. Using 5-D building information modeling (BIM), a model of the proposed project can be built with time and cost incorporated for project owners to see the full scope of a project—both monetarily and visually. After fully coordinating the models and running them through clash detection, all project participants can readily access these models through 3-D model rendering mobile applications in augmented reality (AR) and virtual reality (VR) for construction planning and progress. Finally, to-scale 3-D printers will print not only construction materials but entire structures on-site.
While it is not yet cost-effective nor widely available at the needed scale, 3-D printing will change how we build. It’s up to us to implement the technology that ensures how we build will change for the better.