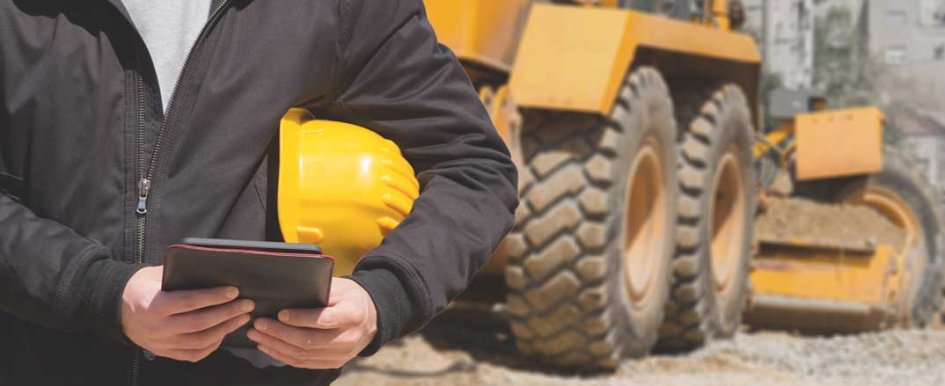
Employees operating heavy machinery know the dangers surrounding working with tools, many of which have the ability to scorch, cut and tear metal in an instant. Unfortunately, simply knowing the dangers doesn’t mean that accidents won’t happen. The best way to prevent accidents is by ensuring that employees have the instruments and information they need to handle machinery with caution. As companies are still adjusting to the OSHA fine increases that went into effect on August 1, 2016, there is no doubt that equipment manufacturers and construction companies of all sizes will continue to be affected by the new rules. Companies of all sizes should be concerned, considering a serious violation penalty, which was originally $7,000, jumped to $12,600 once the new rules went into effect, and willful and repeat violations went from $70,000 to $126,000 per violation.
The new maximum penalties haven’t been raised since 1990, and must now account for inflation in accordance with the Federal Civil Penalties Inflation Adjustment Act Improvements Act of 2015. As the new rules and fines went into effect, North American equipment manufacturers and construction companies had to act fast to ensure OSHA compliance. Unfortunately, it is likely that not all businesses caught up in time, and could risk paying significant fines down the road. Thankfully, mobile technology can help streamline processes and address some of the biggest issues companies face as they try to adjust to the new rules.
Effectively Communicating Jobsite Hazards
As one of the top OSHA violations cited by the National Safety Council, hazardous chemicals have the potential to cause serious safety hazards in the workplace, and are a problem for many. With an estimated 70,000 chemical products used, imported or produced in the United States, Americans are exposed to chemicals on a daily basis. This is why it is imperative that equipment manufacturers get the information they need to inform and train their employees. By adopting real-time, mobile checklists, equipment manufacturers and construction professionals can empower their own employees with the necessary tools to remain safe and injury-free in the palm of their hands. On-the-go compliance has the potential to create a safer workplace, and it is a cost-effective and essential part of early preparation.
Increasing Successful Lockout/Tagout Procedures
The lockout/tagout inspection is vital to tracking the proper safety handling of hazardous energy sources, and is used to ensure that industrial machinery is properly shut off and not restarted until maintenance or service work has been completed. Lockout/tagout protects the health and safety of those who work around industrial machinery and equipment. Ignoring proper lockout/tagout procedures can mean the difference between life and death for equipment manufacturers and employees. By deploying a digitized checklist app, employers can ensure their workers are all working from the same, real-time information and have a clear route to success when handling the energy transfer process. Instead of relying on paper checklists, going mobile is an easy solution for staying on track when dealing with electrical, mechanical, hydraulic, chemical, thermal and other sources of energy used in the manufacturing process.
Machine Guarding in Real Time
Safety checklists are only as good as the person filling them out. When it comes to machine guarding, if information about equipment remains lost on paper, it is not helping anyone. It’s even worse if the person is rushing through his/her procedures, which could lead to employees tripping on-site, or worse, losing a limb.
Considering the rate of amputations in the manufacturing sector is 1.7 per 10,000 employees, following proper procedures is important. Data can be an invaluable asset in machine guarding, and is especially important when it comes to preventing harmful and potentially lethal accidents from happening. By tracking and consistently evaluating processes and procedures in real time, equipment manufacturing teams can instantly share corrective actions that need to be taken to ensure they are not only staying OSHA compliant, but also keeping workplace injuries at bay. There is a lot at stake when it comes to preventing the OSHA compliance fines, and one of the best ways to ensure the safety of your machines and your employees is through regular safety inspections. Forms often get lost or forgotten, and the biggest mistakes happen when someone is tasked with retyping information from paper forms into a software or database program. Mobile technology provides the means to instantly collect, share and learn key compliance details in real time to stay up to code and improve operations. Once a form is digitized, all employees have access to it, regardless of location or time of day.