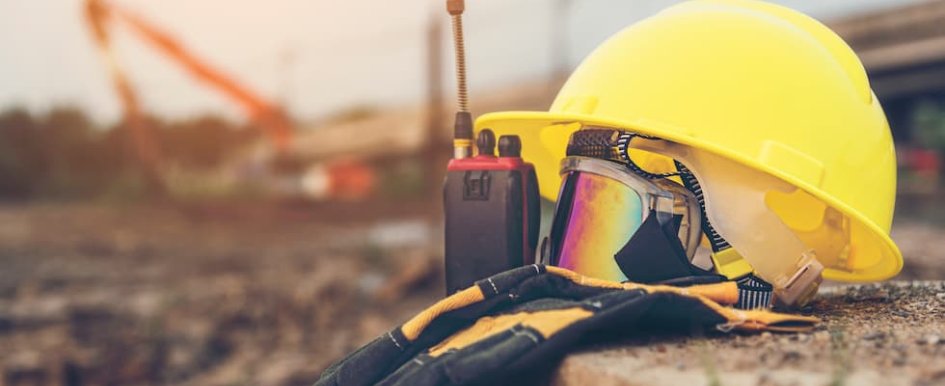
Richard Harvey
Vice President
ICS Commercial LP
The most important factor for jobsite safety in a small commercial construction company is a strong safety culture in which everyone is committed to following safety protocols and procedures. Other important factors include proper training, clear communication, hazard identification and assessment, and the use of personal protective equipment (PPE). It is also important to assign a dedicated safety officer to oversee safety on the jobsite, invest in necessary safety equipment, develop a detailed safety plan, hold regular safety meetings, and encourage a culture in which workers feel comfortable speaking up about potential hazards or unsafe behavior. By prioritizing safety, a small construction company can reduce the risk of accidents and injuries on the jobsite.
James P. Laurie III
Corporate Counsel
ECC
Senior management buy-in to safety creates the culture that ultimately pervades on any project site.
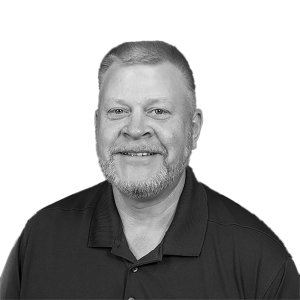
Tom Larson
Project Manager
Centrex Construction
I believe the answer is awareness. In today’s world, the jobsite can be full of distractions, especially with modern “conveniences” such as cell phones. We’ve all seen him — the guy in full PPE, operating a lift or excavator and yapping on the phone at the same time. Companies may employ strict policies against cell phone use on a site, especially for personal use, but abuse of these policies often gets overlooked under the guise of the “work-life balance” they are trying to promote from the office. This can be an issue. Add to that all the technology in construction software that draws our attention away from our surroundings and to a screen instead while walking a jobsite. Ultimately, safety is the responsibility of the individual. Setting your own boundaries on phone and electronics use and limiting other common site distractions will increase your awareness of your surroundings and will greatly increase the odds of you and your coworkers going home to their families at night.
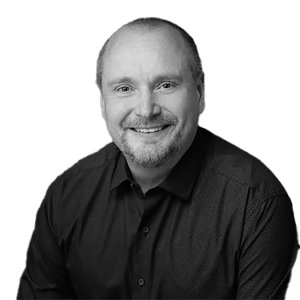
Dan Vandehey
General Manager
Inter-Pak Supply Inc.
The most important factor for jobsite safety is awareness. Awareness is the product of training, information sharing and open inquiry. Without awareness, other safety measures are rendered less effective, or even ineffective. PPE, for example, may be useless if the person using it was never trained to identify the appropriate equipment for a given task or to properly fit and wear it. In addition, most of the safety measures we employ in the workplace are human-executed processes, from the rules governing the use of material handling equipment to evacuation procedures executed in the event of an earthquake or fire. If a worker is uncertain or unaware of the appropriate process to follow in a hazardous situation, they present a danger to themselves and others.
The sharing of information is also crucial to a successful safety program. If a piece of equipment is failing in a way that presents a danger to workers, reporting the failure to supervisors and coworkers is instrumental in preventing injuries. Posting information about potential dangers can effectively warn workers of hazards they may not see for themselves.
Lastly, open inquiry provides for a productive exchange that can identify hazards and prompt training and the exchange of information. Employees should be encouraged to ask questions about practices as they relate to safety. If workers feel they are unable to challenge process conventions, this breeds a culture of complacency where safety issues can flourish.
The mind is the most important piece of safety equipment any worker carries. Every employer should acknowledge that the mind is a vessel, and it is impossible to retrieve something from a vessel that was never placed in it. If workers are to be aware of hazards and the actions they need to take, their peers and leaders must make sure they have the correct training and information, and that they have the freedom to ask questions and start conversations about safety in the workplace.
Whitney Pyle
Chief Operations Officer
JGBowers Inc./Advanced Cabinet Systems
Clear communication of expectations and rules is the most important factor. We live in a diverse world, so ensuring safety expectations are clearly communicated in multiple ways (written, discussed, text messages, clearly displayed signage and warnings, etc.) and in multiple languages is a must. In this day and age, we cannot just expect that people will know what to do or how to work safely. Expectations must be clearly and regularly communicated in multiple ways.
Jonathan W. Thomas
Director of Human Resources
PowerTek LLC
It has been our experience that dedication to safety from the top down is the most important factor. When all employees are aware that management emphasizes, stresses and is concerned about all aspects of safety in all meetings, on all jobsites and at every turn, they take safety to heart. It becomes a company culture of safety first, which in turn produces an excellent safety record. Ours begins at new employee orientation, instructions complete with a safety manual and carried through with weekly on-site safety meetings. New project briefings also include the safety aspects of that particular job. Our safety committee constantly promotes safety certifications and reviews any safety incidents. Safety is always a topic at all employee meetings. Should an injury take place, all employees are aware that it means an automatic drug test and safety review.
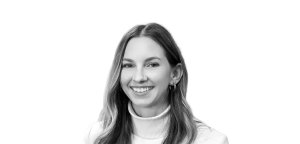
Teresa Sims Johnson, CPHR, HSA
Director, Human Resources & HSE
IMARK Architectural Metals
Like many things in business, we believe that people and culture are central to an organization’s enduring success, and this belief extends to safety on the jobsite. It is no secret that safety performance can affect a company’s ability to tender projects, receive funding, and even attract and retain talent; yet many organizations still see safety programs as a necessary evil that they must abide by to operate. This is not the case at IMARK. Here, we believe that by focusing on education and training of our workers at the onset will result in both project and safety success. Experience has taught us that these core values are more important to the overall prosperity of our safety program when compared to programs built for compliance and behavior-based rewards systems.
Moreover, we want to ensure that workers have psychological safety in the workplace so that they do not fear reporting, nor will they fear bringing ideas to the attention of management. Ultimately, we know that many of our workers are experts at their craft and have great ideas of how to improve their jobs in a safe manner. If we can work together to achieve safer and improved results, why wouldn’t we?
In 2012, we acknowledged that a new generation of worker was increasingly joining our team, and we needed to adapt our safety processes to keep these workers engaged in our program. We moved our safety reporting documentation from paper and pen to a mobile app. This move was beneficial on multiple fronts. The younger generation of workers were able to avoid what they felt were mundane and antiquated reporting processes, and veteran workers embraced the change after decades of doing it the old way. They also were able to provide feedback on documentation performance and add some elements that they felt were missing from the former reporting process. Lastly, this move allowed our supervisors and general contractor partners to receive real-time data faster, more accurately, and with greater usability.
Ultimately, we feel that any organization can create a robust safety program at the field level but if there is no buy-in from ownership, management and the people on the ground, compliance will be minimal or contrived — which does not lend itself to the overall goal of a safe jobsite.
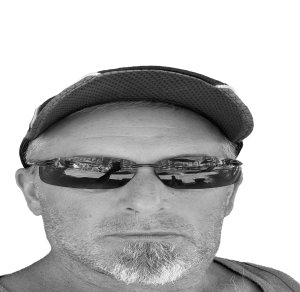
Greg Barker
Environmental Health & Safety Manager
HC Contractors LLC
Communication is hands-down the most important factor for jobsite safety. This can come in the form of job hazard analysis (JHA), daily toolbox talks and reviewing company safety policies. No job or construction site is the same — they all have their unique hazards, and that’s why it is so important to communicate these hazards with everyone working or visiting the jobsite prior to their potential exposure. The jobsite changes frequently, and so do the hazards associated with the progression. A solid communication program will keep the workforce informed of any new hazards that have surfaced during the progress of the project. We all know how important communication is in our personal lives, so why should that differ on our jobsites?
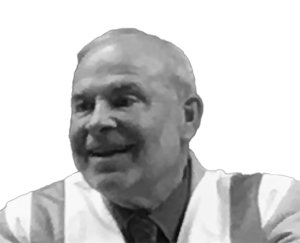
John J. Meola, CSP, ARM
Safety Manager
Pillar Inc.
To answer your question correctly, there is actually no one thing that is most important. If we try to hang our hat on one element, it’s just not going to work. But if I had to name one thing, it would be crystallized in one word: leadership.
Technically, the top three elements should be:
- Leadership
- Employee involvement
- Continuous improvement
There is a textbook worth of reasons for these three elements, because each brings its own food chain of building blocks. Traditional thinking in the safety business tends to be rules-based compliance and system fixated. This mindset achieves very little in the way of incident prevention, but it’s a common method of running safety programs, particularly on construction sites. I see this practically every day. It’s an exercise in regression analysis, but that’s how our industry is programmed to roll.
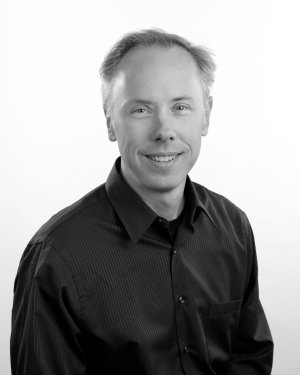
Jaime Vos
Director, AEM Safety Materials Program
Association of Equipment Manufacturers
Building a culture of safety within an organization is key. It means all employees are fully committed to achieving safety in the workplace, and that they take personal accountability for the safety of each other.
Organizations can empower their employees to create a culture of safety by implementing the following practices:
- Understand the existing culture of your workplace and your employees’ attitudes toward safety. Identify areas for improvement and create a plan that outlines specific goals and objectives. Get everyone behind the plan and communicate their role in making it work.
- Ensure that your organization’s leaders are championing the cause. Make sure your employees feel valued for their safety contributions and that they have the necessary materials and resources to do their work safely.
- Provide training that illustrates the employees’ role in the culture of transformation, not just learning new skills. Use the opportunity to promote the employees’ proactive commitment in making the safety culture stronger.
- Track results and communicate progress. Ensure that employees are owning the process improvements and bringing recommendations forward to implement.
- Make safety a priority every day. Implement frequent toolbox talks, employee feedback sessions and bite-sized training opportunities. Overcommunicate policy changes, safety protocols and procedure updates. Give employees the opportunity to ask questions and clarify concerns.
Safety training with all its intricacies, local and state requirements, and Occupational Safety and Health Administration (OSHA) regulations can be difficult to navigate. Businesses can ensure a safe workplace when leaders and employees make a personal commitment in championing a culture of safety. When goals are established, trained to, measured, and truly owned by everyone working together, the company will be well positioned to improve safety across the organization.
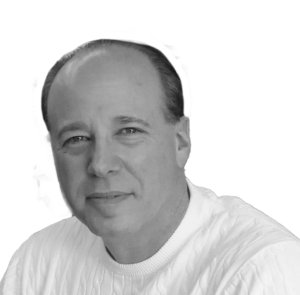
David Balkan
CEO
Balkan Sewer and Water Main
Simply put, the No. 1 factor for jobsite safety is the company’s culture. Proper PPE, a well-maintained fleet, modern equipment, proper jobsite setup, etc., will not provide the optimum results if a company’s culture accepts that jobsite injuries are just the nature of the beast. A culture of working safely within a company has to be all-inclusive and fully embraced. That often means safety committees that meet regularly and contain the full range of stakeholders. Safety meetings should be conducted in an open and nonthreatening environment. Action has to follow the words, and safety initiatives should be routine and reoccurring. Folks want to be recognized, with their safety suggestions welcomed and rewarded.
Annual companywide safety days are also a great idea. If the upper echelons of a company are not committed and passionate about safe work practices, one cannot expect the other stakeholders to be either. A proper company culture of jobsite safety is therefore first and foremost to achieving a safe workplace.
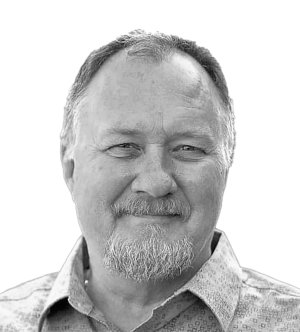
Ken Easley
President
Empire Builders
Awareness of everything around you is the most important factor for jobsite safety.