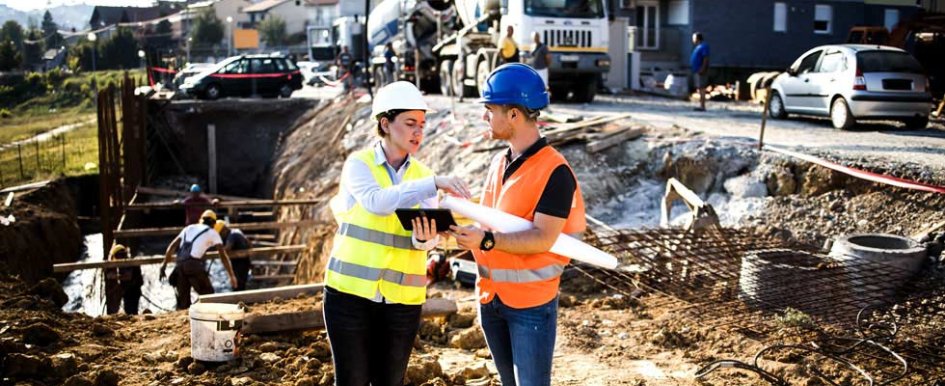
The biggest variable in construction is labor. Too many contractors finish their projects over budget on labor when crews work more hours than estimated in the bid. If your construction company self-performs work with your own crews, the key to success is making sure you bring in those labor costs on budget. When budgeted hours spill over the allotted amount, the crew foreman generally blames such cost overruns on bad estimates, while the estimator and project manager blame slow performance on the foreman’s lack of accountability, poor planning or inexperienced crews. Who is right?
Let’s take a look at some of the possible causes of crew project labor costs finishing over budget:
- Accountability — Employees are not being held accountable to keep labor hours on track.
- Goal setting — Crews and foremen may begin work on a project without having first established labor goals.
- Cost monitoring – The contractor or team lead does not monitor costs until after project completion, if at all.
- Tracking labor — Job labor costs and hours are not tracked, shared or updated weekly with crew foremen.
- Estimating — Estimated bid hours are not accurate and overtime work is not included in the estimate. The estimator neither observes crews on-site nor solicits input from foreman regarding performance timelines.
- Documentation — Change orders are not being documented, approved or paid.
- Planning — Lack of preparation to manage issues in the field, such as: conflicts, poor plans, weather, more move-ins and phases than anticipated, broken or missing tools and equipment, materials shortages, rework, callbacks, punch-list work, and jobsites not being ready when crews arrive.
- Boundaries — Offering the favor of free work to customers, friends or other contractors.
- Review — Lack of final review covering labor hours (estimated vs. actual).
While materials and subcontractors generally come close to budget, construction field labor usually runs about one-third to one-half of the total job cost for most construction trades.
The average poorly run contractor will finish projects from 5% to 15% over budget on labor. For example, they bid at a 10% net profit rate and only make 2% to 5% net profit when complete.
Why? It’s often a lack of focus on labor goals. The easiest method for lowering job costs is to start a productivity improvement program by taking small, simple steps to correct your labor profit-reducer problems one by one. Each step or standard will reduce your costs by small percentage points, which will add up to large overall improvements that make a real difference.
Imagine you set a goal to improve your company’s annual field labor costs by 10%, which only equals to six minutes per hour. Could you make a commitment to achieve a goal of shedding six minutes per hour? And would it really help your bottom line enough to make it worthwhile? Let’s walk through the numbers in Figure 1.
Most self-performing contractors under $10 million to $20 million in annual sales aim at achieving a 5% to 10% net profit goal at year-end. By focusing on hitting labor goals, most contractors can easily make an additional 3.3% net profit and hit their annual goals.
Targets & Tracking
It’s impossible for construction foremen and crews to hit labor targets when they don’t know what the targets are. You must track labor weekly to improve field performance and meet budgeted labor hours. Consider the following:
- Have the foreman review the bid plans and talk to the estimator before bidding projects.
- After winning a bid, hold project turnover meetings and have the foreman, project manager and estimator set an agreed upon labor hour budget for the project.
- Provide foremen with a clearly written job-cost labor-hour breakdown by cost code for their upcoming projects.
- Update and track your team’s labor scorecards weekly and review with the foreman.
- Hold weekly on-site meetings with the foreman, project manager and superintendent. Review the actual versus estimated labor hours, and then the estimated final labor hours versus the budget.
- Hold meetings weekly to review the labor performance results from each project.
Improving Labor Production
Improving field labor costs starts by identifying which areas are bogging down or holding back the crew from operating at their maximum capacity. These productivity pressure points are caused
by many field project factors, including poor planning, lack of supervision, untrained crews, lack of materials,
waiting for decisions, bad attitudes, mistakes, out-of-sequence workflow, broken or lack of proper tools and equipment, missing materials and lack
of standardized field systems.
The average construction field crew wastes around 2 to 4 hours per day starting late, finishing early, looking for materials, waiting for instructions or trying to look busy. To get started making your production fix-it list, try observing your crews for a full day. Get to the jobsite before they arrive and be the last to leave. Take a look at their times (starts, ends, lunches, breaks), site conditions (cleanliness, organization, tool care, storage), site layout and logistics (location and distance to and from the toilet, trash bins, power poles and access gates), distractions (cellphone use, smoking on-site, frequent meetings or check-ins) and productivity (active, productive work performance versus waiting for assignments).
Finding simple ways to fix these problems is not hard. Gather your field crew and ask for ideas and input on how to improve productivity.
Start with establishing and agreeing upon standardized companywide project work rules.
Follow the McDonald’s Rule
As a construction business coach, I often facilitate meetings with field foremen and superintendents to help companies decide how they want to do business and develop field standards to increase overall field productivity. When we start, many foremen don’t want to deal with a set of standard rules or have to manage their crews on difficult-to-enforce items. But in reality, these factors and pressure points can add up to lots of wasted dollars. When employees know what the rules are, they follow them.
I always remind them of “The McDonald’s Rule.” If employees at McDonald’s aren’t allowed to do it, we can’t either. For example, at McDonald’s, if an employee is late, he doesn’t keep his job for long. McDonald’s employees can’t smoke or use the cellphone while working. Additionally, if they exceed the allotted break or lunch time, they receive a warning, and their pay is docked. No excuses and no exceptions. There’s no reason it should be any different at a construction company.
By implementing these simple field standards and tracking systems, you can improve productivity by 10% or more. Get your team involved and start a competition to find ways to save money by being more organized, planning better, tracking progress and setting simple and clear standards for everyone to follow.