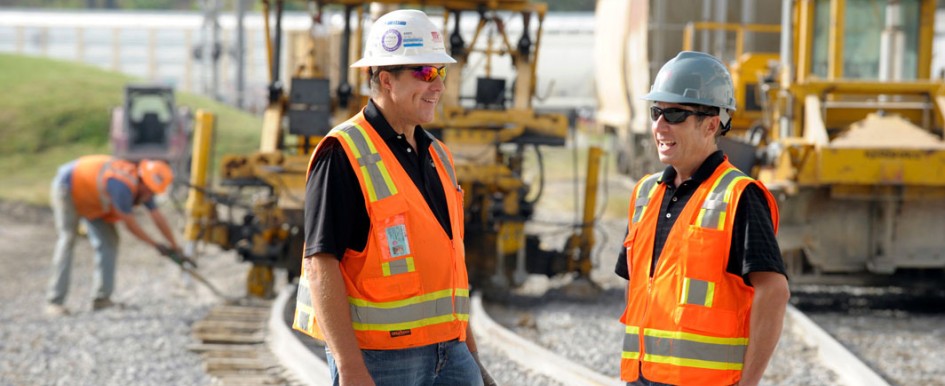
The modern jobsite is rapidly changing. From remote-controlled machinery to augmented and virtual reality, construction business owners are leveraging technology in new ways to increase efficiency, reduce costs and make smarter decisions.
These new capabilities make the jobsite safer, which decreases the need for owners to worry about machines breaking down or having malfunctions on the job. Ultimately, a safer work environment can mean less equipment damage or employee injuries, which can lead to lower insurance rates across fleets.
A 2014 LexisNexis study found two thirds of small fleet managers shop for insurance at least every 2 years—and more than a quarter indicated interest in implementing telematics for insurance purposes. Why? Because telematics increases equipment security and improves driver behavior, ultimately alleviating many of the challenges that come with equipment management.
With the construction industry expected to reach a value of $10 trillion by 2020, fleet owners are smart to turn to technology that can help them optimize their businesses and keep them at the forefront of the innovation needed to meet skyrocketing growth. Those owners looking to integrate telematics can take a page out of the playbook of Musselman & Hall Contractors LLC, and reap the impending benefits to their fleet utilization and bottom line.
Musselman & Hall’s Path to Telematics
Musselman & Hall is a contractor in architectural concrete, asphalt paving, structural concrete, concrete flatwork and railroad construction and maintenance based in Kansas City, Missouri. Today, the company is owned by Doug Hall, Dexter Phillips and Mike Morris, and employs more than 275 employees during the busy construction season.
Musselman & Hall’s pain points on the jobsite are similar to most companies of its size. Asset allocation and management, controlling labor costs and balancing internal rates with billing and progress on customer jobs are the most common issues for the company.
Even more, the company made a $13 million investment in equipment, making it crucial to ensure employees are operating equipment properly and safely. Musselman & Hall made the strategic decision to turn to a telematics solution provider to help address its pain points.
Providing Insight into Risky Equipment
The role of telematics in driving insurance costs down starts with the foundation of 360-degree insight across a company’s entire fleet of equipment. But by integrating a telematics solution, Musselman & Hall can now track the location, health and use of its fleet—trucks, heavy-duty vehicles and heavy equipment, regardless of manufacturer—in real time and through one platform, giving leaders the necessary data to address business challenges.
For example, telematics has helped Musselman & Hall protect its equipment investment. By sending proactive monitoring and customizable alerts for improving asset health, contractors now have the actionable insights to better manage and use equipment. Armed with this data, the company can reduce risk and downtime and prevent catastrophic failures that can drive up insurance costs. If a piece of equipment is failing, telematics also supports automated service and maintenance, helping prevent critical breakdowns and costly repairs and rentals.
However, telematics provides more value to a company than just mitigating risk and preventing breakdowns. Musselman & Hall has also been able reduce fuel costs and automated fuel reports, like the International Fuel Tax Agreement (IFTA), by having insight into excessive idling and unnecessary miles driven. The telematics data has also allowed the company to bill its operators and other personnel more accurately by leveraging real-time location and run-time data down to the second.
Guarding Equipment Day & Night
In 2014, the average estimated value of a stolen piece of equipment was more than $46,000. In the same year, law enforcement received 11,625 heavy-equipment theft reports, and only 23 percent of that equipment was recovered. Just as telematics can help owners identify risky machines, this solution can also be used to track and monitor equipment to prevent theft, vandalism and unauthorized use.
Musselman & Hall has seen this value firsthand. By having real-time location mapping and remote lockout and receiving geofencing and time-fence alerts, it has been easier for contractors to prevent theft, recover assets and detect unauthorized usage.
Instead of searching for replacements when parts of their fleet go missing, contractors can use telematics to pinpoint the location of a machine days after it was stolen. By integrating surveillance systems with telematics platforms capable of providing real-time GPS locations, contractors can quickly begin a seamless recovery process, and thereby limit their losses.
Additionally, keypads integrated with telematics serve as an advanced option for fleet owners. The second any equipment breaks its geofencing boundaries, the keypad can send a notification directly to an owner’s laptop or smartphone. From there, he/she can remotely shut the machine down, rendering it useless to potential thieves.
While theft prevention is important, it is not the only thing contractors can do to preserve fleet safety and security. Equipment damage, as well as employee injuries resulting from unauthorized use, can prove to be just as costly.
By combining a security keypad that utilizes a telematics platform with existing asset compliance software, owners can ensure equipment doesn’t fall into the wrong hands. Each user will receive a unique identification code to start up keypad-equipped machinery.
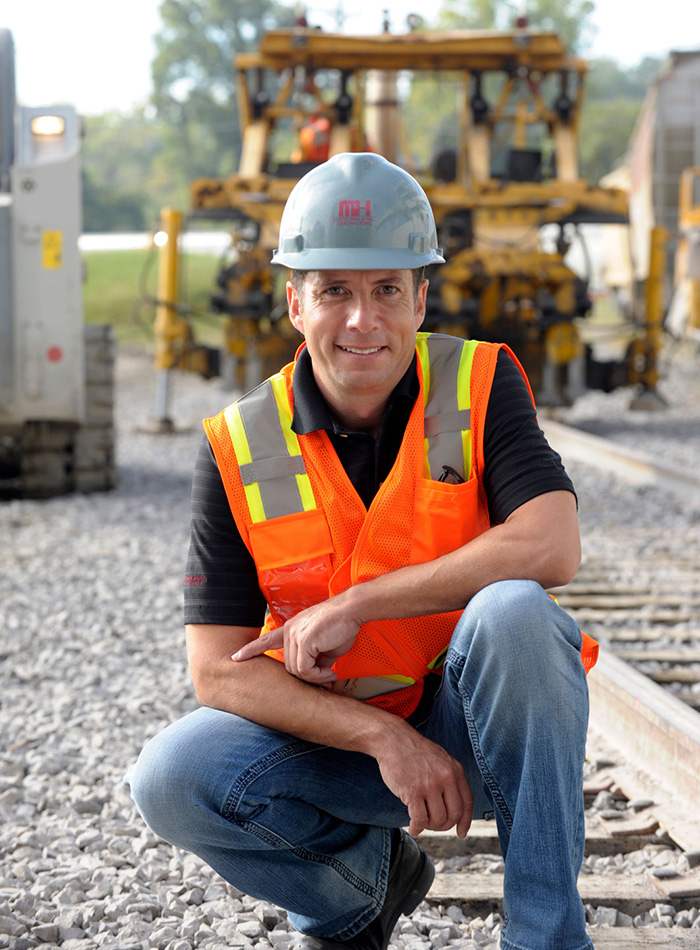
Owners can also integrate telematics with their human resources (HR) systems to ensure only workers with proper certifications can use the equipment.
Regardless of whether they are on the jobsite or not, telematics helps managers rest easy knowing their assets are being operated only by those who are properly trained and certified.
This means less worrying about accidental damage or the liability that comes with another worker using equipment without permission—helping keep insurance premiums low.
Considering the average annual cost of equipment theft is about $400 million, it is necessary to stay protected. If equipment is stolen, GPS tracking data from telematics can ease the recovery process. Having a single platform to track all equipment ensures a stolen or severely damaged piece of machinery won’t hike up insurance costs.
Keeping Workers Accountable & Safe
The construction site is notorious for being dangerous, even for the most skilled workers. In fact, there are roughly 150,000 injuries on the jobsite per year, and 1 in 5 worker deaths are in the construction industry. But with proper safety measures and the help of telematics, fleet managers can improve overall safety on the jobsite.
By utilizing telematics, fleet managers can identify and eliminate risky behaviors that put workers in danger. And ultimately, these tech initiatives can result in reduced liability and lower insurance rates for your company. For example, by receiving real-time location mapping and speeding and aggressive driving alerts, Musselman & Hall has been able to identify which workers exhibit poor driving behavior.
From there, the manager can outline steps for improvement, or reprimand accordingly if it is a continuous problem. This capability has not only helped mitigate risk, but has also protected drivers and operators from false claims and preserved the company’s brand image.
Telematics also opens up the possibility of automating workers’ risk profiles. Owners can set a knowledge baseline for an entire fleet and define parameters for how to score operator behavior. This can be applied to a variety of factors, including speeding, idling or braking speed. With telematics, construction managers can see when activities deviate from the baseline.
This also helps for keeping workers accountable. Operators are incentivized to use equipment more safely when they know their managers are monitoring their driving habits. This could drive down the accident rate on the jobsite, and, in turn, insurance costs.
With the ability to better manage equipment, identify problem behavior and prevent theft, contractors can use telematics to their advantage, especially when it comes to reducing insurance rates. Since about 75 percent of fleet managers said saving money on commercial auto insurance was extremely important to them, it may be an investment worth making. Telematics creates a better system for equipment management, as well as fleet security, saving on costs down the road.