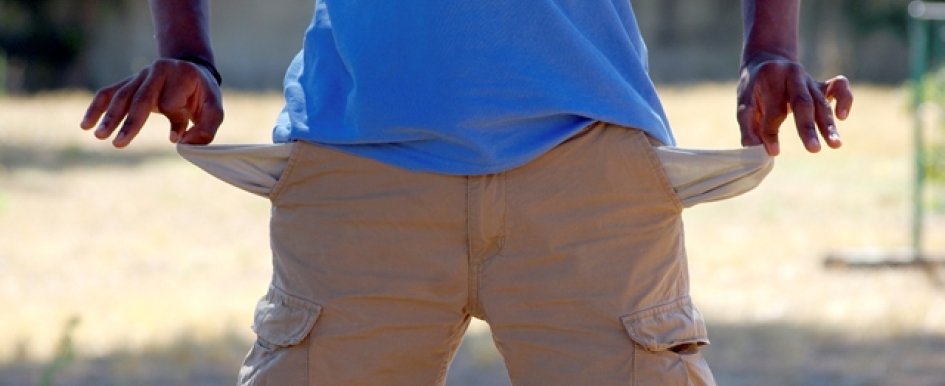
With the many economic challenges facing construction firms today, it is imperative that companies optimize their operating efficiencies. Saving time and money should be a top priority for anyone in the construction industry trying to stay competitive. The following are three of the biggest issues that construction firms currently need to address to stay afloat.
1. Building Construction
According to the 2016 Dodge Construction Outlook, residential and nonresidential building is rising 16 percent and 9 percent respectively from 2015; however, nonbuilding construction will be retreating 14 percent from last year. Gas plants and electric utilities will also fall 43 percent after jumping 159 percent in 2015. Construction companies involved in gas plants and electric utilities are likely seeing a decrease in the number of available jobs this year.
2. Employment
During the recession, a significant number of employees left the construction industry and never returned. The ramifications of this have been widespread—even today, there are many companies that still struggle to staff teams with skilled labor. As a result of the labor shortage, many construction companies will be forced to be more cautious and selective about the size and number of projects they will take on at the same time. They may also have to provide higher wages to attract more skilled workers.
3. The Flip Side of Low Oil Prices
Low oil prices are often considered to be a good thing, but the negative aspects of these lower prices are starting to reveal themselves both in the United States and abroad. In the U.S., there is the direct economic impact of the laying off of thousands of oil workers and the collapse in gas and oil capital expenditures. These losses contribute to oil’s massive ripple effect on construction, trucking, metals and the army of businesses that partner with gas and oil. As the year continues, it is possible that these industries will also experience a decrease in employment and projects that can be attributed to the low oil prices.
One Way to Save Money Right Now
One way to improve your company’s bottom line right now is with effective, efficient tool control. Instead of paper and Excel-based spreadsheets and extra tool room staffing, an automated tool control system can reduce the burden of labor shortages by allowing you to run a tool room with fewer staff and save money by not having to replace lost or stolen tools nearly as often. You can then spend your newfound savings in areas that your business needs most.
Tool and equipment management and tracking systems can handle checking tools and equipment in and out, as well as tracking the transfer of equipment to various tool rooms and jobsites. The ability to manage tool inventory remotely can significantly save construction companies time and money. Put simply, tool and equipment tracking and management software quickly provides you a return on investment through:
- Reduction in tool hoarding and equipment losses
- Tool control and inventory reconciliation
- Time saved during tool check-in and check-out
- Time saved by not searching for misplaced or lost tools
- Increased productivity because workers can find the right tool at the right time
Your Tool Control System
While the right tool inventory and tracking system will not be the answer to all of the economic challenges a construction company might face, it could be an important part of the overall solution. Improving your company’s bottom line, improved productivity and efficiency, increased job satisfaction and more positive outcomes are possible when you implement an effective tool control system.