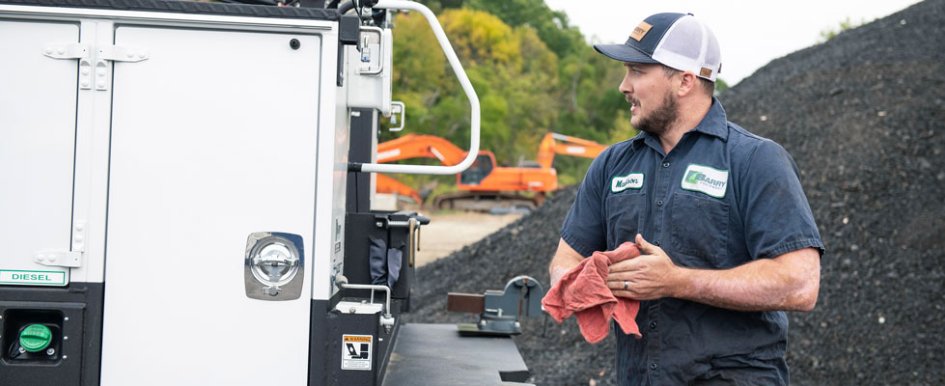
Machine maintenance is key to getting the most out of your construction equipment. That might seem obvious, but how you decide to manage and complete your maintenance isn’t always as straightforward.
If you are weighing your options for managing your machine’s preventive maintenance, there are some considerations to keep in mind. Remember, the goal of preventive maintenance and programs is to identify issues before they cause machine downtime, not fix them after.
Couple a preventive plan with your daily maintenance plan to help maximize the life and productivity of your equipment, including excavators and wheel loaders.
Start from the Beginning
The best place to start is your equipment’s operation and maintenance manual and the recommended service schedule. These documents can help you understand what actions to perform for your machines. They also give a schedule for when the maintenance items are due.
Your equipment will determine the exact preventive maintenance you will need to complete — but there are some general guidelines to follow. For example, filter changes, oil changes for your engine or hydraulic systems and transmission upkeep. Take a look at what machines are in your fleet. Determine what specific needs are required. Then, consider the number of machines you use. These can help you evaluate which preventive maintenance plan works best for you.
It’s important to note that these service intervals should not replace daily upkeep. Daily maintenance is something to stay on top of, regardless of your preventive maintenance schedule. Having a plan for machine checkups should be in addition to daily maintenance. That includes walking around the machine, making sure it’s greased and topping off fuel and diesel exhaust fluid (DEF).
The next step is to keep a management system for tracking your maintenance needs and schedule. This may look different for everyone, from low-tech paper or board tracking systems to high-tech telematics. Regardless of what you use, having a tracking system will help you stay up to speed on what’s required at the key hour intervals on your equipment.
Once you’ve done the initial work of determining what is needed, you can look at how you want to go about doing it. Your service options include outsourcing or hiring a technician. Both have their pros and cons. There’s no right answer, but there are definitely things to consider.
Keep It In-House
If you choose to keep all your preventive maintenance in-house with a technician, there are some benefits. For one, you are in control of the schedule. You can be proactive and do tasks early or wait a bit; whatever works with your upcoming schedule.
Another benefit is knowing the costs upfront. An in-house technician is salaried. You know your labor costs throughout the life of your fleet. You can also factor in the maintenance costs of parts if you know their costs.
Choosing to keep things in-house with a technician also lets you find the perfect fit. Maybe you have two types of equipment and you can hire someone who specializes in them. Taking the time to find a qualified person who blends well with your fleet and staff can be worthwhile.
Unfortunately, technicians are few and far between these days. Finding a good technician, bringing them in-house and being able to keep them is a challenge for construction companies. It is a challenge that some dealers face as well.
If you work with a dealer, there’s less risk. The dealer may always have an option for you to backfill your service needs if your technician leaves.
Opt for Outsourcing
Dealerships can offer support and resources if you utilize them for your preventive maintenance. If you’re just starting or are about to start a relationship with a dealer, make sure you are clear about your schedule and maintenance needs. Most dealers can and will work with you to accommodate your calendar and preferred maintenance schedule.
Once a preventive maintenance program is established, working with the dealer and scheduling becomes easier. Dealers can use the machine’s telematics system to identify maintenance needs and schedule the work when it fits you best.
Successful dealers typically receive specific original equipment manufacturer (OEM) training from the brand of equipment that they are selling. They can know from just their trained eye what to look for as they’re checking the machine. One of their jobs is to then identify any concerns that can impact the functionality of the machine later.
This in-depth knowledge is beneficial when paired with telematics data. In some cases, the information can be used to identify machine cycles and trends. Telematics also helps the dealer and owner understand how fast hours are being accumulated, so you can plan and schedule tasks more efficiently. Telematics also helps owners keep track of hours from a warranty standpoint. Telematics provides valuable information for a service department. Dealers routinely check telematics to monitor their customers’ machines. They understand the data and how to utilize it to improve their customer’s day-to-day operations.
Another factor to consider is the environmental responsibilities associated with maintenance. Environmental requirements should be followed. Waste oil should be managed properly in accordance with local regulations. The same goes for machines with diesel particulate filters (DPFs). In DPFs that need to be reconditioned or replaced, the ash should be disposed of properly.
Since dealers work on machines daily, they have the know-how and processes in place to make sure the waste is disposed of properly.
Some dealers have mobile lubrication trucks and can safely perform fluid changes in the field. If scheduled correctly, a trained technician can change fluids in multiple machines on the same day. If you want another option, there are also third-party companies that just service heavy equipment. Their entire business model is to service customers that don’t have a technician and have chosen to outsource.
One reason to consider this method is if you have different brands of equipment. It’s also an option if you are located far away from your dealer. That process will be similar to having a dealer do it for you; it’s just a different business that’s doing that on behalf of your fleet.
Find What Works for You
Finding the right preventive maintenance plan, coupled with daily maintenance, can help maximize the life and productivity of construction equipment.
When it comes to your daily and regularly scheduled upkeep, the biggest thing is consistency. No matter what you select for preventive maintenance, make sure it works best for you.
There’s a break-even point at which bringing a technician in-house might make sense. And there’s a break-even point where it’s better having an external person do the work, whether that is a dealer or a third party. Every situation is different. It all depends on your fleet size, the type of machines and their utilization rate.
However you choose to manage your preventive maintenance, utilize your dealer to set up the plan. Dealers are a resource to help ensure you have a plan that works for you. Though a dealer may have a vested interest in doing the maintenance themselves, they also understand the needs of a customer and can make sure to find a good balance.