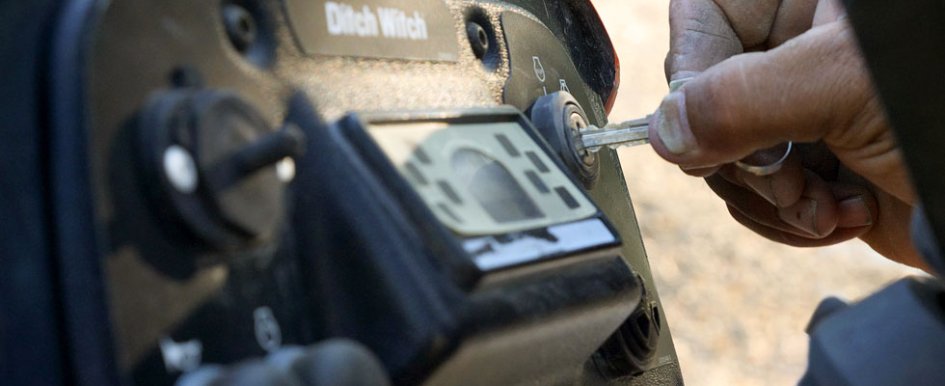
The success of your construction business hinges on the reliability of your assets. Both your productivity and ability to complete projects are reliant on the healthy functioning of such assets. And since construction fleets have notoriously high procurement and operating costs, costs must be managed to maintain your bottom line.
To do this, you must understand what to include and how to determine total cost of ownership (TCO) with the assistance of fleet management software. Knowing your fleet’s TCO will allow you to make data-driven decisions when it comes to preventive maintenance and replacement strategies. TCO expenses are broken down into fixed and variable costs. Fixed costs are predetermined regardless of asset usage such as leasing or registration expenses. Variable costs, on the other hand, are subject to change depending on the size, usage and overall efficiency of the fleet.
Rely on Software to Determine TCO
Technology helps fleets automate processes that otherwise bottleneck efficiency. Cloud-based fleet management software presents a cost-effective solution with a tremendous return on investment. It empowers you to become more accurate and effective while providing insight into your operations. It does this by providing structure to process and data entry so that data can be harmonized, and insights easily drawn out. What used to be a mess of paper, receipts, spreadsheets and phone calls becomes organized line-item detail about the inner workings and status of your fleet.
Without reliable insight into operating costs, a business simply couldn’t sustain. Purchasing an asset may be costly but is only the beginning of the operating cost cycle and tracking that cost is essential. The myriad benefits of software culminate with the ability to calculate and analyze TCO in an efficient, reliable manner. Additionally, using software to determine TCO has the added benefit of providing you with more time to focus on other tasks.
The Costs You Can Control
Outside of a replacement strategy, there isn’t much that can be done to combat depreciation. It’s an inevitable occurrence and cost that is unfortunately absorbed. That said, there are ways to control some of the variable costs. Best of all, it’s the two that impact a fleet the most: fuel and maintenance.
Regardless of the current price of fuel, having a system to track fuel costs and monitor consumption for each asset is critical to success in the field. The
high expense of gasoline and diesel is ever-present for your construction equipment and vehicles. Monitoring fuel costs is the most effective way to identify inefficiencies and potential savings in your fleet — and even combat fuel theft. You can drastically reduce fuel expenses by measuring your construction fleet’s fuel use and fuel efficiency.
Managing your assets’ fuel use enables you to identify equipment idle time and improve driving habits. You can reduce your fuel consumption not only on-site but also while traveling between sites by controlling asset idle time and establishing driving behavior guidelines.
Monitoring fuel theft can also lead to fuel savings. Integrating your construction fleet management software and GPS tracking solution allows you to make comparisons between fuel transactions and actual vehicle locations. Locations can then be flagged if they exceed a certain distance threshold.
Fleet management software provides fleet managers with necessary cost analytics while streamlining the collection of fuel data to better manage costs. It’s no longer necessary to wait for drivers to return fuel receipts at the end of the day and spend hours logging them into spreadsheets. Instead, fleets can have drivers input fuel entries via a mobile application or automatically collect data through fuel cards. Fuel cards can be integrated with fuel management software, allowing the data to flow seamlessly from the time of the fuel purchase directly to the cloud-based software, without the need for any data entry or calculations.
Tracking the true cost per mile or cost per hour of use, depending on the asset, is another benefit of fleet management software. This will give you a detailed understanding of how much an asset costs on a relative scale and provides clarity when trying to develop a budget. It can also help determine your return on investment from assets.
Estimating Annual Maintenance Costs
Maintenance is essential to maximize the lifecycle and return on investment of an asset. The median cost of annual maintenance for an asset is approximately $2,626. This average encompasses routine preventive maintenance across a variety of asset types including vehicles, buses, trucks and heavy equipment. This can become a large expense for your organization when you look at spending that amount on every asset each year and possibly more.
With fleet management software, you no longer have to rely on mundane and tedious paperwork. Instead, invoices and work orders can be generated and transmitted electronically.
If you conduct maintenance in-house, you’ll be able to provide technicians access to the software to receive notifications to conduct maintenance when an asset reaches a certain point. These levels can be customized based on mileage, hours or use — or triggered by an issue logged through a digital inspection.
From there, you’ll be able to track completed work and monitor the costs so you can shop around for the best vendor prices and determine maintenance’s impact on TCO.
Since your construction fleet has diverse assets ranging from pickup trucks to heavy-duty equipment, it can be difficult to keep track of the varying maintenance schedules. Falling behind on maintenance can lead to asset downtime, higher expenses and reduced profit.
Fleet management software allows you to set maintenance reminders based on asset type to proactively manage your diverse assets and prevent unexpected failures and accidents.
Using software to manage your fleet maintenance allows you to automate workflows, eliminate entry errors and maintain a well-organized, easy-to-access maintenance history. It can also help you maximize the lifespan of vehicles and equipment, while managing cost and risk.
Unplanned Downtime
In your industry, vehicles are not just a mode of transportation, but a critical component to job function. Another important cost to consider is unplanned downtime. If an asset is unavailable, the impact on a business can be tremendous.
The opportunity cost lost to complete a job or service is only a portion of the lost revenue. Wages still need to be paid regardless of productivity — but that isn’t the worst of it. One of the biggest risks of unplanned downtime is the loss of new business. The timing of a new opportunity is unpredictable. But having assets ready to perform when called upon is the best case to ensure you won’t lose potential business. You can’t take on a job if your equipment isn’t available or in proper working order.
With fleet management software, you can not only track vehicle assignments to ensure every vehicle is being used to its fullest capacity, but you can also automate preventive maintenance reminders. Downtime risk can be mitigated with a formal preventive maintenance schedule that ensures your assets are getting the repairs and maintenance required for optimal performance.
Remember, the total cost of ownership is always evolving. Your costs will constantly fluctuate based on your variable costs, and it’s imperative that you routinely monitor and generate reports to avoid any surprises.
Calculate TCO to Determine Fleet Expansion & Replacement
Even though fuel and maintenance are the highest individual costs, collectively, they only make up about one-third of TCO. Why is that? It’s because fuel and maintenance are variable costs, where fixed costs such as the initial purchase price and annual depreciation account for the highest fleet costs for construction companies. For example, a new 2021 Ford F-150 costs $29,290 and since the average vehicle loses 20% of its value in the first year of ownership, the depreciation of that truck would cost you $5,858 in the first year.
Compare that depreciation cost to the annual fuel cost for a Ford F-150 at $3,698 and it’s easy to see the impact depreciation has on TCO. This further emphasizes the importance of developing a plan for asset replacement.
No matter where you see your fleet in 2022, understanding your true total cost of ownership will provide you with insight into your assets and allow you to make smart decisions based on real data.