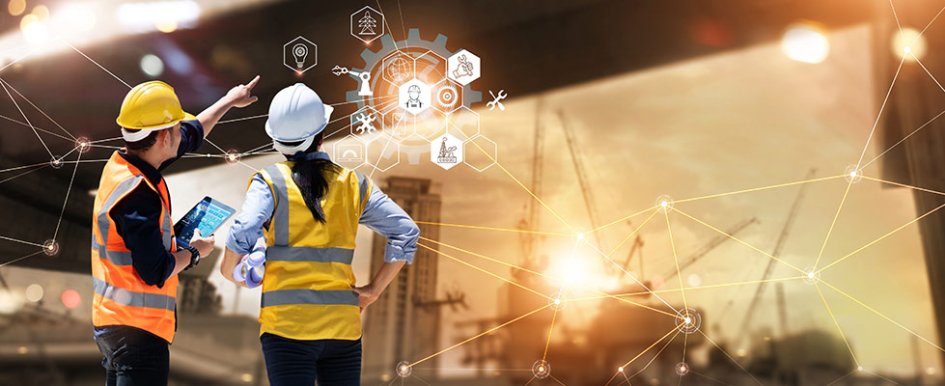
Artificial intelligence (AI) can bring benefits to the construction industry. But like any new technology or equipment on a jobsite, you need to learn how to safely operate it to get the most from the investment.
Based on conversations with executives at midsized and large construction companies, it’s clear that AI is already boosting productivity. For example, consider the complexity of a large-scale construction project and the need for accurate, real-time information across every aspect of the build. This includes finding and assigning skilled labor, ordering and tracking supplies, filing proof of compliance and more. Every part of the project has multiple steps, many of which can be automated and streamlined using AI. This has proven to be a considerable time saver. In construction, minutes equal dollars, so any time efficiency and productivity can accelerate project timelines without compromising safety, it is a win.
But there is a catch.
Getting a return on AI requires the underlying data to be accurate, consistent and current. When data comes from a variety of sources, such as apps downloaded on a jobsite, ad hoc forms or a spreadsheet, there is a higher likelihood of inconsistency. Even if these tools and apps are driven by AI, they are faster — but poor-quality data will not produce highly valuable insights. Remember, AI is an evolutionary technology, constantly being trained and improving based on the input it receives.
Now imagine that same large-scale construction project has information about a delay in the supply chain. That detail is kept separate from information about the availability of skilled carpenters available on a Tuesday. When the carpenters show up on the assigned day, they find they have nothing to do because of that delay in supplies. The cost of this oversight is significant, and it is especially frustrating knowing the issue was avoidable. If the information in digital tools and apps is not brought together in a cohesive way, it increases financial, operational and safety risks.
When considering the risks of AI in construction, they typically fall into three areas.
1. The Risk of Gray Work
The first risk, and the one with the strongest ripple effect, is known as gray work — the time and resources lost using workarounds, ad hoc solutions, and other processes when technology and established methods won’t work for you. A common symptom of gray work is time and resources lost trying to reconcile various sources of data and information located in a variety of tools and apps. Gray work makes it hard to collaborate, effectively manage all the parts of a project and make the right decision in a timely manner.
To address gray work, take a closer look at the technology being used in the office and on the jobsite, and look for redundancies, workarounds and information silos. Bringing information together on a dynamic work management platform makes it easier for employees to find what they need, when they need it, at the speed and scale of the project.
2. The Risk of AI Reliance
The second risk, ironically, is overreliance on AI. This may not seem possible in construction, where the end product is a physical structure, but it can happen when AI is viewed as a replacement for work, as opposed to a way to augment and streamline project management.
AI cannot replace all the functions of a construction project, but it can automate time- and resource-intensive tasks such as scheduling, approvals and reporting. And we have all seen examples of how AI can reduce the risks of jobsite accidents by sending robots into risky or hard-to-reach areas, or by identifying failing or soon-to-fail equipment based on maintenance records and equipment life spans. But every job still requires laborers, project managers, site supervisors and others to make sure the work gets done properly.
How do you know you have an overreliance on AI? You will know if decisions are made solely based on AI recommendations and/or your team is unable to accurately assess a situation and make the right decision without the aid of AI.
3. The Risk of Not Managing & Optimizing Data
The third risk is not effectively managing and optimizing the data being generated within projects and across the company. When project teams are using AI-driven tools and apps to streamline processes, and those insights are cohesively brought together to eliminate gray work, the next step is to use the data to run an even more efficient construction business. Otherwise, you’re accumulating mounds of data and missing an opportunity to get ahead of potential project delays.
As data grows throughout the company, accelerated by AI, you will need to properly manage and analyze it. This allows you to identify unseen patterns and predict likely outcomes based on a continuously learning AI model.
For example, consider that constructing a new wing on a hospital typically takes your team 24 months. AI-driven insights can analyze past project milestones and spot potential delays based on previous interactions with suppliers, sourcing skilled labor and local inspector protocols. Knowing about potential setbacks leads to smarter bids and more accurate project plans.
Another benefit of proper data management is training AI models on your construction processes. Since so much of construction is local or regional, adapting the models to how your business works can be a significant productivity boost.
After attending last fall’s big construction trade shows and working with construction decision-makers around the globe, it’s clear that AI will have an even bigger impact on the built environment. While it offers productivity boosts, making the most from your investments in AI requires a strategic plan that is realistic about the benefits and the risks.
The next and final article of this three-part series will explore real world examples of how AI in solving the gray work issue in construction.
Check out the entire series:
- Part 1: Reality Check: Using AI in Construction
- Part 3: Coming soon