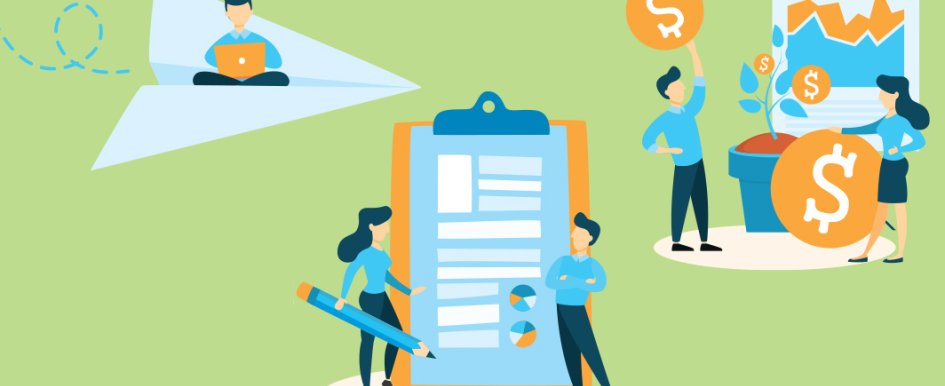
Waste is all too common on construction projects today. That waste is not only bad for the environment, it also cuts into budgets and diminishes a project’s overall return.
The mindset of, “order more than we think we'll need" is one of the most common causes of construction material waste. For example, concrete contractors often order extra formwork components just in case, but those components often go unused and become construction waste. The same is true for electrical cable and duct piping, both of which are often over-ordered to avoid a reorder that could cause project delays.
Inefficiency also results in substantial waste. Overlapping tasks, rework and running over budget and behind schedule all result in wasted productivity. Often, poor planning and a lack of communication is the root of this problem.
There are certain tasks on a jobsite that need to be completed before the next subcontractor can come in to do its work. For example, if a team shows up to install drywall, but the electrical work hasn’t yet been completed, work stops. With the skilled labor shortage, trade workers are booked out for months, so rescheduling can be difficult and have a ripple effect across the project.
In order to eliminate waste, boost productivity and truly enable a connected team, changes must be applied to the entire supply chain. A growing number of construction companies are turning to a constructible process in which all phases and trades are connected, models and workflows are content-enabled and data-rich constructible models drive smarter workflows. A constructible approach can move the needle on eliminating waste by:
1. Facilitating real-time collaboration and communication among all stakeholders
It’s important to break down communication barriers and encourage collaboration across project teams. Being connected is the greatest defense against the inefficiencies that stem from data locked up in silos. Enabling shared access to data among multiple stakeholders allows them to collaborate, review and make changes to a model together in real time.
2. Delivering more accurate data to limit rework and standardize processes
Constructible content simplifies the development of comprehensive models for each trade and makes construction data more useful in feeding downstream work processes. This helps to save time, money and effort by avoiding unnecessary rework. Data-rich models of each component required can provide more than just geometry to include up-to-date data, such as weight, sourcing and cost to streamline build of materials and ultimately the supply chain.
3. Leveraging historical data to improve future performance and estimates
A key element to making improvements is to learn from experience. Data is a key element in driving optimization, predictability and automation. Experience is your intellectual property and a differentiator for your business, if you use it correctly. Are you capitalizing your data to optimize and improve planning? The best start is to inventory the data you possess and data that you could collect. It’s important to build a culture that values experience as a core asset.
4. Automation drives increased efficiency
With sophisticated machine control and robotics, models developed by engineers are now directing the earthwork, fabrication and layout in the field. Likewise, with constructible data, processes like estimating and project scheduling can all be automated in ways that dramatically reduce work cycles. Importantly, trade partners no longer need to recreate building data and can easily federate their work with the project.
5. Enabling connected workflows
The constructible process helps unify project phases with a connected workflow in which each project member has access to shared project data including models, so they are able to see exactly what other team members are seeing. Fully connected workflows allow constructible data to be shared by key stakeholders for use in fabrication, estimating, location-based project planning and more.
Constructible at Work
Forward-thinking construction companies like Barton Malow and The Weitz Company are leveraging technology and the constructible process with great results.
The Constructible Process is helping Barton Malow increase efficiency by developing constructible models earlier in the process, then using that data to automate production including fabrication. As a result, Barton Malow now details and fabricates 15-percent faster than before.
The Weitz Company had a goal to reduce the common "big building wastes" of material overproduction, nonproductive waiting time, defects and rework. Moving to a constructible process and BIM resulted in a 22-percent reduction in rebar waste alone.
A constructible process helps streamline construction throughout all phases of a project, eliminating waste and leading to increased efficiency, predictability and productivity. As more companies embrace this approach, it will lead to continual improvement and push the construction industry forward.