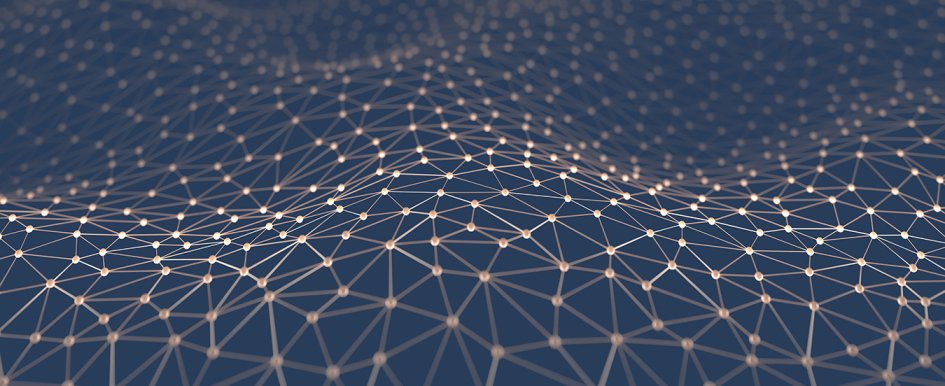
In the current construction market, one of the key indicators of a company's future success is its ability or inability to adopt technology. And regardless of where your company stands in the implementation of various tech solutions, you should have a firm understanding of how your company could benefit from a completely connected jobsite.
To help with that, CBO recently talked with Jim Lynch, vice president and general manager of the Construction Business Unit at Autodesk. Lynch is responsible for managing all aspects of operations within Autodesk's Construction Business Unit, including product design and development, marketing, sales and customer success. Lynch joined the Autodesk team more than 20 years ago, and has held a number of leadership roles within the company. See his insights below.
CBO: What issues do you see currently with the connection between technology used on the jobsite and during the construction project itself?
JL: Disconnected data—data living in silos—is one of the larger problems we hear from customers. There are a lot of unique point solutions in the market, but many of these interesting startups and apps are disconnected from a common data platform. These siloes increase risk for contractors because if something changes on the jobsite—and changes are a part of the building process—it is challenging to reconcile the changes across the many apps and data silos. The owner works with architects and engineers to change the designs, but it doesn’t immediately transfer to the field because the software solution the contractor is using is so fragmented.
It’s great to have all of these different software providers building these solutions, but you have to know how you will best manage the data. You want project information to be accessible, at any time and from anywhere. This information needs to be live and fluid from the beginning of the project to its finish. And solutions may be coming for these silos—it’s definitely a space that has a lot of attention from investors right now.
This is why Autodesk created an integration program for our BIM 360 construction management platform which allows partners to integrate their technology on our platform so our customers have all of their data in one place – accessible anytime, anywhere.
CBO: How can technology connect the entire project from start to finish?
JL: At Autodesk, we focus on improving safety, quality and efficiency through the use of our technology. We are the first company in the market to have a fully connected platform to manage data and information from conception to preconstruction through construction and handover on a single, connected platform. The BIM 360 platform connects design teams with contractors and subcontractors through the full project lifecycle. Teams are able to collaborate in real-time in the cloud. A single platform housing all data and project information provides additional value to project owners who will have a wealth of data to use for operations and maintenance of the finished project.
Additionally, with the platform, we are providing several different modules, depending on what tools and data the contractor needs to access on any given project. The platform is customizable, and it’s possible to build tech, including the integration program, on top of what the platform currently offers. Customers get the big picture – not just pieces of information in many silos.
CBO: What will be the biggest challenges for business owners that have yet to implement technology that connects all of the moving parts on a project?
JL: Adopting technology across the enterprise is becoming more of a requirement than a luxury to remain competitive. However, we suggest to our customers that they learn to walk before they run by taking the time to learn new tools; you have to learn new tools and ensure that if a cultural shift is needed internally. Your processes will be better when they are digitized and automated. And sometimes, this can truly be a bottom-up approach. We often see someone in the field who has a vision of how tech can play a role in benefitting a project, and that person will drive the adoption of the solution. Sometimes, though, it’s the executives. Ideally, you want both, but that is not always the case because change takes time.
Right now is like the perfect storm for the adoption of tech like the BIM 360 platform, though. There is more work, and at the same time, a skilled labor shortage. For digitization, you first need the infrastructure—mobile tech and the cloud. But now that many in the industry have the infrastructure, it can move forward with the next phase.
CBO: What parts of the project do you see having the most potential for improvement through the use of new technology?
JL: First and foremost, we want contractors to get to work, do their jobs, and get home safely to their families. Safety is our number one priority for our customers. Period. Technology such as Autodesk’s Project IQ deploys machine learning to analyze data provided by a customer to understand the safety risks on a project with the goal of reducing risk to people on the jobsite. We all know the “fatal four” in construction, but technology is really stepping in to improve safety.
Change management. How do you deal with a change on the project? Things change constantly. But by bringing a real-time connection to all of the teams involved with a project, technology is really making a difference in how a jobsite is run.
Another tech trend is the convergence of the manufacturing and construction industries, which is already demonstrating success in decreasing risk across the full project. All of the forecasts for the future of work in our industry are incredible because of the urbanization that is happening around us. Many companies are looking at taking a manufacturing approach to construction, which has the potential to improve many aspects of a project, but also to help mitigate waste – construction projects represent 30 percent of the waste in the world.
Modular and prefabricated construction represent an opportunity to cut that waste significantly. The automation of off-site offices, and the implementation of the internet of things on construction projects will be a big factor in how companies push ahead of competition.
These examples truly represent the future of making in the building industry.
With the increased use and adoption of modular and prefabricated construction, you may be wondering how your company could benefit from adopting these processes. Cannistraro, a mechanical contractor based in Boston, Massachusetts, is a leader in modular construction technology. Click here to learn how Cannistraro is using Autodesk products to aid in its prefabrication processes. Watch the video above to hear from Cannistraro's Kelly McNeill and see part of the company's modular construction process.