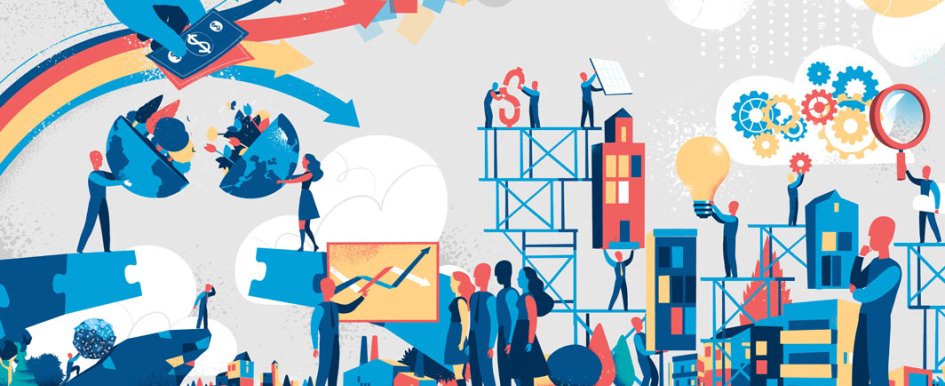
There’s a reason construction was reputedly slow to adopt digital technology compared to the aerospace, automobile and semiconductor industries. Mainframe computers were too costly and required too much overhead for all but the largest construction firms to deploy in their home or field offices. In addition, foremen and project engineers on the jobsite could not use desktop and laptop computers, so they stuck with paper-and-pencil processes.
However, this has changed dramatically in the last decade with powerful and easy-to-use mobile phones and tablets and with data networks available almost everywhere for sharing real-time data between field and home office systems. Construction’s years of deliberate lag in adapting to digitization made the industry ripe for new tools to accomplish goals faster, more accurately and, of course, more economically, as well.
With more contractors embracing this movement, through adopting specific jobsite tools or construction tech ecosystems, such as Autodesk’s BIM 360, and with construction making Investopedia’s “Top 10 Fastest Growing Industries in the United States” list, the future looks bright for the industry. And that means it’s also bright for investors and venture capitalists (VC).
What Investors Want
VC firms employ different strategies and focuses for a variety of their investment decisions. Banking on technology, some VCs employ a strategy that focuses on early-stage companies redefining efficiency in three areas of construction: the built environment (design, construction facility operation, management), transportation/logistics and renewable energy/grid management.
According to TechCrunch, investments in these areas have become increasingly popular. The site reported that, in 2018, funding in construction startups jumped 324% over the previous year, resulting in $3.1 billion in overall investments.
The construction industry can be viciously cyclical, but many industry investors are looking beyond short-term goals to invest in the future of the space. Many VCs don’t focus their investments on specific projects but, rather, on the companies that help engineering, construction and real estate firms achieve dramatic improvements in the life-cycle cost, schedule, safety and sustainability of their projects.
These investors seek to create “triple bottom line” sustainability in terms of economic, environmental and social sustainability goals and metrics that can be broken down into three categories.
- Economic—Startups like Pype and Rhumbix represent a convergence of hardware, software and business model trends to save even midsize construction firms millions of dollars annually by eliminating the information disconnect and delay between the office and the field.
- Environmental—Startups like Ultra High Materials LLC are developing next-generation materials and innovative manufacturing processes for construction that create far less wastage of natural resources. These companies are producing almost zero carbon dioxide (CO2) emissions in their manufacture, assembly and operation, compared with traditional materials and processes like cast-in-place or precast concrete, as well as the manufacturing, fabrication and erection of structural steel.
- Social—Startups like Safesite Solutions Inc. use emerging information technologies to detect and correct safety hazards. Jobsites, by nature, can be dangerous places. Moving data from the field to the office in real time allows management to oversee, monitor, compare and access information that keeps workers and businesses better protected.
Greener Building Processes
Perhaps what holds the most promise is the way builders and contractors are looking to the future with regard to their materials and building processes. Leadership in Energy and Environmental Design (LEED)-certified building has gone from an anomaly to a trend too big to ignore. In 2006, 296 LEED certifications were awarded.
In 2017, that number was over 65,000. LEED is quickly becoming a preferred metric for evaluating buildings, due in no small part to its life cycle financial payback. The life cycle operation, maintenance and renovation of buildings typically accounts for eight to 10 times the cost of their initial construction.
Contractors who develop a reputation for sustainable building through greener practices—such as delivering buildings with measurably lower life cycle costs due to higher energy efficiency, enhanced durability, resilience to natural hazards and a lower volatile organic compound release—are becoming the favored builders for many building owners and operators.
These owners and operators are often looking for a sustainable future that includes carbon taxes, or carbon cap-and-trade regimes. Moreover, they’re considering their own reputations in order to attract and retain a workforce and set of customers who are increasingly more environmentally concerned.
Greener Building Materials
Climate change is motivating both mitigation and adaptation, which is clearly playing out in the construction industry. One material that highlights the upcoming shift in building processes is concrete.
Cement is arguably the most environmentally unfriendly material on earth. Its manufacture typically uses fossil fuels to heat kilns that drive CO2 out of limestone, creating double the negative impact on emissions.
Cement’s manufacture, transportation and installation account for about 7% of all greenhouse gas emissions globally. Finding replacements for ordinary Portland cement that can match or exceed its properties as a binder for concrete, as well as its cost, has been a key objective for environmentalists.
Novel cements are proving to be just as effective in concrete as a building material, but they have not yet been cost competitive with cement, so they have not seen widespread adoption. But that is changing as companies like Ultra High Materials are inventing new chemical compounds that can bind sand and aggregate into concrete with faster set times, higher early strength and better durability than Portland cement—all at a comparable cost.
As of now, there are only a handful of big producers of alternatives to cement. With a lack of competition comes slower integration, but this slowness is mainly due to reluctance from owners, architects, engineers, building code officials and contractors to adopt new materials that have yet to withstand the test of time.
Caution has to be part of the equation, as the stakes are so high. However, reluctance can also trigger stagnation. Many business owners were reluctant to adopt time and management (T&M) tracking. But the evidence became clear that digital T&M tracking was saving big money by cutting down on misplaced tags and time-wasting preparation.
VCs routinely bet on the future. And, right now, they’re betting on the construction industry—an industry that is not only showing its ability to adapt, but also to embrace new technologies that will allow building to take place faster, safer, more effectively and less expensively.
Healthy skepticism can be valuable because it forces you to look carefully at all the potential costs and benefits of new technologies. And when you do, you’ll see that stagnation is something to avoid, and the future of construction is now.