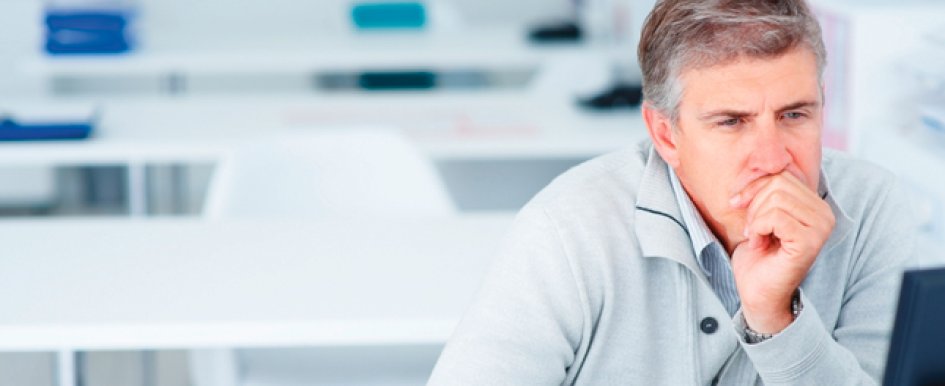
Building Information Modeling (BIM) is gaining ground as construction participants recognize the benefits of computer modeling. However, participants should enter this new modeling world recognizing that these opportunities come with costs and risks. Understanding the risks associated with BIM can help contractors manage and make the most of this new technology.
In a parable from the Indian subcontinent, six blind men touch different parts of an elephant, and they each form a different observation. In the same way, participants from six different BIM projects might describe dissimilar benefits that arise from varied modeling activity. Each of those projects also could have involved different modeling costs, levels of effort and degrees of participant interaction. These differences arise because the participants are seeing the variety of benefits BIM offers. Differing benefits offer participants a challenge: They must understand the expectations for modeling, which will determine modeling behaviors and the cost and risks associated with BIM for that particular project.
For example, some modeling can be done simply by one entity. If BIM is to be used only for marketing, for instance, the designer or contractor can create simple models or views for the owner without much additional cost or risk. An individual general contractor can also perform clash detection, but the cost for this purpose is likely to be greater. MEP trades can plan pre-fabrication without coordination with others. Having only one entity involved (“Silo BIM”) reduces cost, coordination and risk.
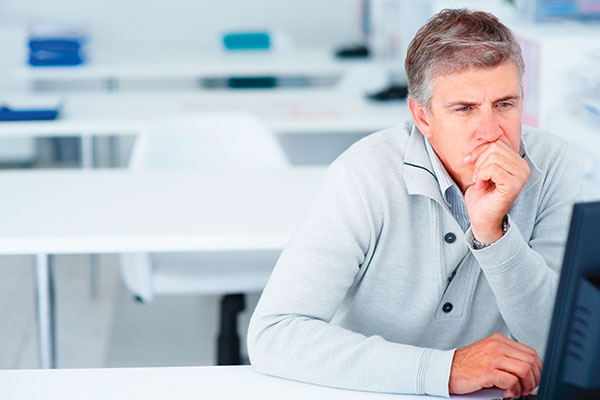
Other modeling expectations will require specific modeling activity for success. If participants want to use “4-D” or “5-D” BIM (incorporating the “dimensions” of scheduling and/or cost), their model will have to identify building elements by location and present building components as they would be built. Consider this example: If a contractor plans to build 40-foot concrete columns in two or more stages, the model should reflect that sequencing. It should divide the column (and rebar) into the planned construction stages so the column elements can reflect individual schedule activities. Again, the anticipated end use dictates the modeling behavior, which also affects the cost.
Some project participants use BIM to allow full-scale design collaboration among designers, the general contractor (or construction manager) and specialty trades. Imagine, for example, a structural engineer working directly with a steel fabricator’s detailer to expedite steel design (and short-circuit the submittal process). Taking advantage of these BIM capabilities involves collaboration among multiple parties, which will drive costs. The collaborators will have to agree on how and when they will transfer drawings, what dimensional accuracy will be expected from each contributor and who will manage the coordination of the modeling effort, which might require an information manager. Additional server space will be needed for the exchange of large files; some projects will use a project website to exchange files, while others will use a CAVE (computer-assisted virtual environment). Modeling collaboration might even drive the contracting format—it is unlikely that full-scale modeling collaboration will occur on a hard-bid project. In short, the expectations for BIM use will affect the cost of the effort as well as the risk involved. Beware of the specification that simply says, “The project will use BIM.”
Liability for BIM Participation
BIM may also create a new risk profile. Imagine that the mechanical contractor suggests resizing duct work or modifying air handling equipment, and this change is later discovered to cause unwanted noise for the end user. Is the mechanical contractor to blame? Should the mechanical engineer have caught the problem? Thinking more broadly, does a contractor’s participation in the design process create an expectation that the contractor must spot all errors in the model? Does it prevent the later argument that the contractor is “just following the plans?” As contractors become modeling participants and contributors, they may have liability for their contributions. Their performance may be judged not only by contractual requirements but also by the tort standards that have long applied to the design profession—did the contractor modeling participant meet the standard of due care?
Technological Complications
Computer modeling platforms have advanced significantly during the past 10 years. However, various modeling participants still work from different software platforms. BIM participants report that data is sometimes lost when transferred from one program to another. This phenomenon is common enough that it has been given a name—“data repurposing.” This name may sound more benign than it is, given the danger that a data recipient will not receive all the intended information in a model and may not even know that it is missing.
Contract Documents
Another potential problem with BIM is that modeling competency among designers and builders is far ahead of building authorities, building codes and even contracts. For example, few building authorities will accept a model for permitting. Therefore, models may have to be reduced to two-dimensional drawings for permitting purposes. Similarly, building trades in the field may not be working from the model. The contract documents may consist of two-dimensional drawings. If defects in performance are alleged later, questions about whether the model is a contract document and which documents have precedence will not be trivial issues.
Managing BIM Costs and Risks
The good news is that many project participants are already managing these risks. Their groundbreaking work, along with industry forms, can help contractors budget the cost and manage the risk. The first rule in managing BIM risk is to understand the end use. Pennsylvania State University’s Computer Integrated Construction Research Group offers a BIM selection worksheet as part of its BIM project execution planning guide. This checklist allows the parties to select possible BIM benefits from a variety of options. Once the participants agree on the modeling’s purpose and end use, they can anticipate their staffing and other costs. They can also manage technological challenges—knowledgeable IT construction professionals understand the software platforms and their interoperability shortcomings. Another important step is to agree on which modeling platforms and editions will be used.
The possible details of a modeling exercise are so varied that the parties are advised to plan the modeling process before beginning. Industry form documents are intended to help with this planning process. These agreements are supplemental contract documents in which the participants describe the following:
- How they will work together
- What documents will be contract documents
- What dimensional accuracy is expected in those documents
- What responsibilities the parties will have to each other
- What indemnities and consequential damages are (or aren’t) available
- Who will be the information manager
- What intellectual property rights will be transferred to facilitate the modeling (and how)
Other documents offer different approaches, but each offers a way to identify and apportion risks associated with modeling. These industry forms are helpful guides to identify risks as well as possible risk allocations and mitigations.
BIM is still in a formative stage. Some of the risks discussed above will be resolved by technological advances, and others are inherent in the changed behavior and collaboration that make BIM so attractive to some. Careful contractors will manage these changed risks and additional costs as they always have by first identifying them and then planning accordingly.