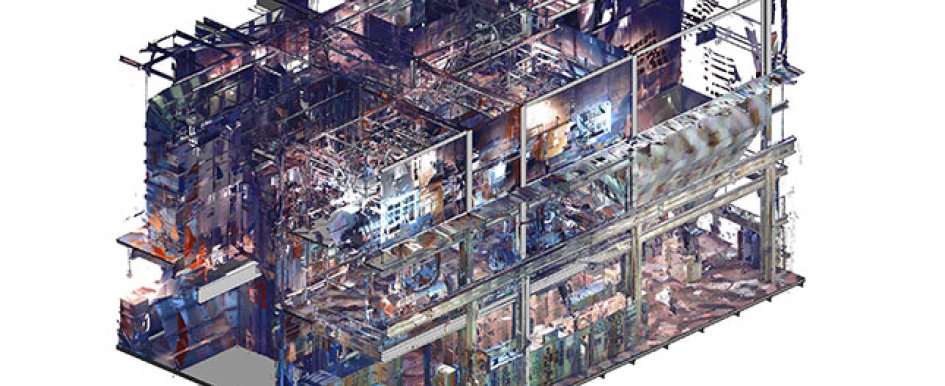
During the last three years, reality capture has emerged as the industry standard for the wide variety of applications and tools that assist in the documentation of existing spaces or facilities. Looking toward the future, it will likely become one of the most implemented technologies in the industry.
The oldest and most common tool used for reality capture is the laser scanner. This equipment, which dates back to the 1960s, first started to catch on as an engineering tool in the 1990s. At first, laser scanners were primarily used in civil engineering associated with horizontal (road and bridge) construction. Today, reality capture has expanded to the world of the general contractor.
The process of laser scanning is fairly simple. The laser is projected from a scanner unit, which resembles many other survey devices, into a space or onto an object. The laser takes millions or even billions of measurements of the space by moving vertically and horizontally until the entire object or space is covered. In a building, this often takes multiple scans. The resulting measurements and the location points are then plotted into the 3-D world based upon a series of targets and reference points, creating a scalable 3-D image of the space or the object. This scan can then be converted into a building information modeling (BIM) format or other file type for a wide variety of applications. As the uses for this technology have expanded, laser scanners are now being put on mobile devices from ground vehicles to drones, furthering its potential.
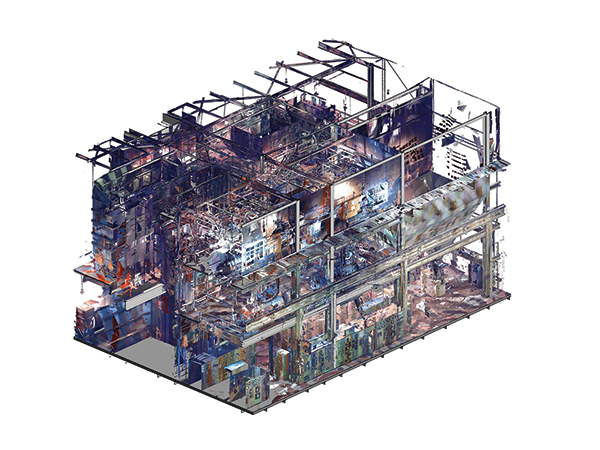
The cost of this equipment has decreased dramatically from three years ago, making it a more common tool on many construction jobsites. A construction worker no longer needs a tripod and an expensive laser scanner. Affordable handheld electronic measuring devices that use Bluetooth technology to link to a laptop and produce a BIM model are also available. Recently, Google announced that, through their Tango Project, they are piloting an application that would allow people to use an iPhone or other smartphone to scan while walking through a space. Although still in beta testing, this application would theoretically allow people all over the world to produce scans of any space, all accessible on the cloud. These continued advances indicate that reality capture is in a state of exponential growth. In an industry that is substantially focused on risk reduction and profitability, reality capture offers contractors several unique benefits. Outlined below are three examples of reality capture’s impact on the jobsite.
Example 1
A small regional general contractor in southeastern Wisconsin was starting a 10,000-square-foot remodeling project at the local hospital. During the demolition process, the contractor decided to laser-scan the existing ceiling mechanical space and use the data to create a 3-D model. With the cooperation of the subcontractors and the design/ engineering team, they combined the laser scan (now in a model) with the original engineering and subcontractor fabrication documentation. Through a series of coordination meetings, the entire team resolved more than 300 potential coordination issues and conflicts prior to the start of mechanical system installation. The result? No requests for information related to mechanical system coordination were issued during the project. The owner commented that this was the first remodeling project that was completed ahead of schedule and without extensive mechanical, electrical or plumbing (MEP) coordination changes.
Example 2
An existing power plant adjacent to a private college campus was donated to the college. The goal was to retrofit the power plant into a student activity center. The college and the designers had the vision to reuse and retain many of the old pipes and equipment as design features. The problem was how to document this space accurately for the design team and the contractors. Taking field measurements and producing drawings would take months with a team of people. Since many of the spaces were extremely high, reaching certain elements to take measurements could be hazardous. In just five days, a team with one laser scanner and two people was able to scan and produce a 3-D BIM model of the existing space that provided the design team and the contractor with accurate existing documentation. The information is accurate to plus or minus 1 inch, and all dimensional data is available from the scan. So, dimensions that were not obtained in the field could easily be pulled from the scan. This was especially critical for the design team from out of state. Not only did they have a BIM model of the existing conditions, components such as the structure could be extracted for further analysis and consideration for reuse.
Example 3
On a large, 14-story hotel that had an accelerated schedule, the structural system specified was post-tensioned (PT) concrete slabs. The problem was that the design for the structure was moving ahead faster than the floor layouts. With PT, missing an opening means having to go back on-site to X-ray the slab core drill or cut the slabs if reinforcing tendons are not in way. Prior to pouring of each floor slab, the steel reinforcing and the post-tension cables were laser scanned to verify all locations with the BIM format. The laser scan of the PT was then overlaid with the latest floor layout to ensure that every possible pipe and duct sleeve was in the proper location. If a sleeve was missing or mislocated based upon the latest plans, a bulletin communicating the required fix prior to concrete flowing was delivered to the field the morning of the pour, allowing the general contractor to avoid a significant risk.
These are just three examples of how this technology can impact projects of all sizes and types at various phases of construction. As the technology continues to develop, reality capture will have tremendous opportunities to improve the construction industry.
Currently, technology companies are beginning to test the following uses of reality capture:
- Existing condition verification prior to the start of construction: A simple laser scan of existing sidewalks, curbs, gutters and adjacent buildings can be a valuable documentation process that mitigates risks. This scan can be used for verification of existing conditions if claims for damage to adjacent elements occur after construction commences. Because the scan is scalable, you can even compare the size of existing cracks to post-construction cracks— a much more accurate tool than photographs that have no scale.
- Progress documentation tool: As reality capture becomes increasingly mobile with drones and handheld devices, a reality capture device could be your documentation tool for jobsite progress. Imagine walking through your building, capturing the current level of completion, loading that into a BIM model and comparing it to the previous week. You will know precisely how much work was completed. As drones and quad- copters become more stable, let them fly through your project at the end of the day to document progress with mobile reality capture.
- Quality assurance: Why not look to the manufacturing industry for applications? On a jobsite, as the framers are completing a wall, a reality capture device could be used to create an image of a framed wall and then feed the precise measurement of the framing layout to an automated drywall cutting device similar to a CNC machine. The machine analyzes the framing in place, compares to model for quality assurance, maximizes the utilization of the sheets of drywall, cuts the pieces, labels them and produces an installation drawing of the pieces, resulting in less waste, more productivity and better quality control.
If this is starting to sound a bit too farfetched, look at the evolution of the automobile industry in the U.S. Since the 1970s, the American automobile industry has implemented many similar technology principles and is once again a global leader in automobile manufacturing. The construction industry must look to other industries to see how we can embrace new technologies to produce these same efficiencies.