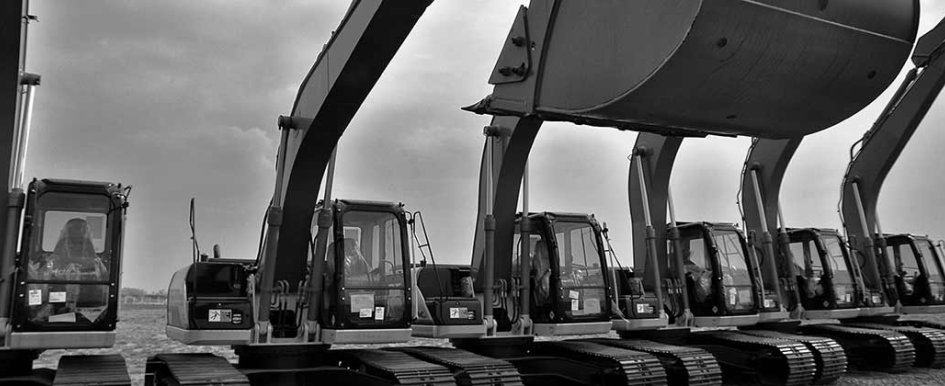
Managing a fleet of heavy equipment in the construction industry brings the challenges of scheduling the equipment, monitoring usage and managing traffic at the jobsite, to name a few. And all fleet managers know that timing is everything on the jobsite.
Coordinating the timing of truck deliveries at a jobsite when a big concrete pour is scheduled means making sure that the trucks arrive in the right sequence at the right time. A fleet management system integrated with telematics provides instant visibility into truck locations. So, if issues occur, solutions can be found easily, decisions can be made quickly.
Real-Time Visibility
Vehicle telematics help a company manage the movement of people, equipment and materials so that every machine and body arrives at the right place exactly on time. Without this visibility, into trucks’ arrival and departure times, as well as raw materials location and status, many problems can occur (e.g. backups in the yard that delay deliveries and can be detrimental to product quality for deliveries of cement).
Knowing where your trucks are in real time can help ensure smooth workflows and schedules. If you know a truck is running late, you can locate and allocate another truck to make the delivery. Consequently, a fleet management system with that incorporates telematics can dramatically improve workflows, scheduling and asset management and minimize risk.
Driver Accountability
Because telematic devices tell the exact location of a vehicle in real time, you can easily see if a vehicle diverts from its assigned path. Does this mean the truck has been stolen along with the cargo? Or is the driver not following his/her route assignment? Does this mean there is an issue with traffic, and the truck has to go around the incident?
Is the driver taking an unplanned break? With telematics and fleet management integrated, whenever a driver diverts from his/her route assignment, you know when and where it happened, allowing you to begin answering these questions.
You can then proactively alert the jobsite that the truck will be delayed so that the project manager can either request another load from another truck, or can begin work on another portion of the project while the team waits for the truck to arrive.
Alerts can also be provided when violations related to hours of service (HoS) restrictions occur, such as taking unscheduled breaks, driving more hours than allowed, or not taking the required 10 consecutive hours off duty. This requires incorporating electronic logging devices (ELDs) into trucks to monitor times of service, but combining ELDs with telematics devices helps to quickly locate the truck and the driver. With the combination of these devices, management has proof of the violation, which can help, if proof in court is needed.
Equipment Usage Data
ELDs and telematics devices can also inform managers when drivers repeatedly brake too hard, speed, accelerate too quickly or drive erratically—information that can be used in a driver debrief, allowing management to pinpoint bad driving habits and discuss methods of improvement. Having a safer fleet helps to mitigate risk, and potentially lower insurance costs.
Monitoring driver behavior can also improve fuel usage. When drivers accelerate too quickly or drive aggressively, fuel is wasted, which can lead to higher costs that cut into your profits. Poor driving habits also affect the usage of vehicles, potentially cutting back on unnecessary repairs—the better maintained a vehicle, the less likely it is to not break down unexpectedly.
If a truck breaks down on the way to a jobsite, the fleet management system can alert project managers in real time so that another truck can be commissioned for service.
Additionally, fleet management software can help you create a continuous improvement program. As data is collected from in-cab devices, analytics can be performed on the data to drive more informed decisions. And better decisions help to mitigate risk and foster continuous improvement.
Fleet management solutions help keep product quality in check for products like concrete that need to arrive at the right place at the right time. Managers can see when the site is ready to be poured, when each truck arrives, when to queue the next truck, and when the job is complete. If any of that is out of sequence, the concrete quality may be poor and become a risk to the building or structure. In some situations, the concrete cannot be used at all—a huge monetary loss.
Fleet management systems empower construction companies to mitigate risks within their operation, helping to improve efficiency, vehicles care and regulations compliance, which all keep the job moving forward on time and on budget.