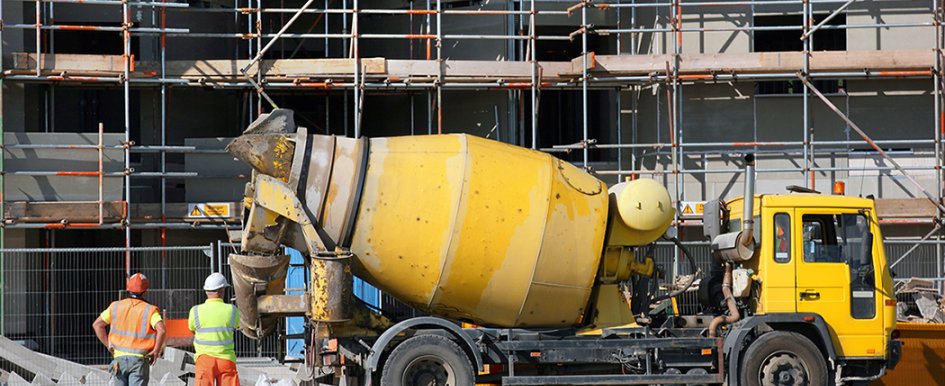
Concrete is expensive. According to the National Ready Mix Concrete Association, the cost of concrete is $108 per cubic yard. On top of this is the cost of delivery fees, truck rentals, driver pay, loading/unloading workers, etc. And this doesn't even include the cost of time spent during the delivery process testing and checking the quality of the concrete to make sure it arrives at the jobsite at the right consistency and quality required for the job.
Significant inefficiencies exist in the transportation legs of construction projects. Any time a truck driver has to climb down from his/her truck to punch in job information, and then climb back up into the cab, inefficiencies occur. If the truck driver waits in line behind a slew of trucks, inefficiencies occur; and at an environmental level, idling at gates or in a line of trucks also uses unnecessary fuel and emits carbon dioxide.
Often, producers will overdesign their concrete mixes to ensure the quality of their final delivered product. Many producers believe wasting money and materials in overdesigns is better than delivering concrete that gets rejected because it is the wrong slump—or worse: placed and then removed. In reality, money spent on the cost of overdesign can take a pretty significant chunk out of the producers’ bottom line.
Industry averages on the overdesign of concrete is about 30%, with 20% being necessary to ensure test results meet specified amounts. For an annual production of 500,000 cubic yards and an estimate of 5% overdesign, your current cement costs on overdesign equals $620,000 annually.
Another contributor to the cost of concrete involves the time lag that occurs when the truck driver must delay delivery to test the quality parameters, including the slump of the concrete load and make adjustments. If producers had visibility into the concrete properties while the load is in transit, then the driver could keep moving and not have to stop the truck, or put himself/herself at risk of ruining the materials by adding unnecessary water or chemicals.
The average cost estimate of one minute of delivery time is $1.37, with the average time to adjust the slump at the jobsite equating to 5 to 15 minutes in every delivery cycle. A single truck delivers about 600 loads/year, so the cost to adjust the load, based on five-minute delays, equates to around $4000 per truck annually. If you have 100 trucks, that’s way over a quarter of a million dollars spend per year for a fleet to make load adjustments at the jobsite. Imagine the savings that could be received if the quality of the concrete would be guaranteed to be just right at delivery.
Tools exist that provide real-time information on the concrete properties of a load. Probes within the truck measure slump, temperature, volume, drum rotation and other information that details the workability of the concrete. The probe sends real-time information to displays within the truck cab, notifying management when the load is ready to leave the yard, when it is ready to be discharged at the jobsite, when water needs to be added, and how much material remains in the drum after discharge.
The data collected provides historical reference for improvement of the next delivery cycle.
By reviewing the load data, producers can evaluate and optimize mix designs, reducing the need for overdesign of mixes. The data can help with disputes to prove quality of the mix. You know that the concrete you delivered was at the optimal quality for the job. The risk of having to replace the concrete already poured can be reduced using the historical information and quality data.
Solutions becoming available in the market, including Command Alkon’s system, mean there is no longer a need to “live with” the guessing game of what is going on with your concrete once it is loaded into the drum of your truck. You can now gain a constant view of the properties of your fresh concrete throughout your delivery cycle as well as capture and archive a historical snapshot of the quality of the concrete you deliver and place.
A reliable, user-friendly system provides visibility into fresh concrete properties throughout the entire delivery cycle and reduces the need to overdesign your mixes, saving money and time within your operations. The delivery efficiencies and material savings that come hand in hand with this visibility allow you to save time and money to pay for this investment in quality.